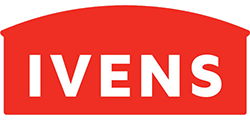
Over Ivens
Ivens was founded in 1930 by the great-grandfather of Peter Van de Perck, who as the current managing director, is the fourth generation of this Antwerp family business.
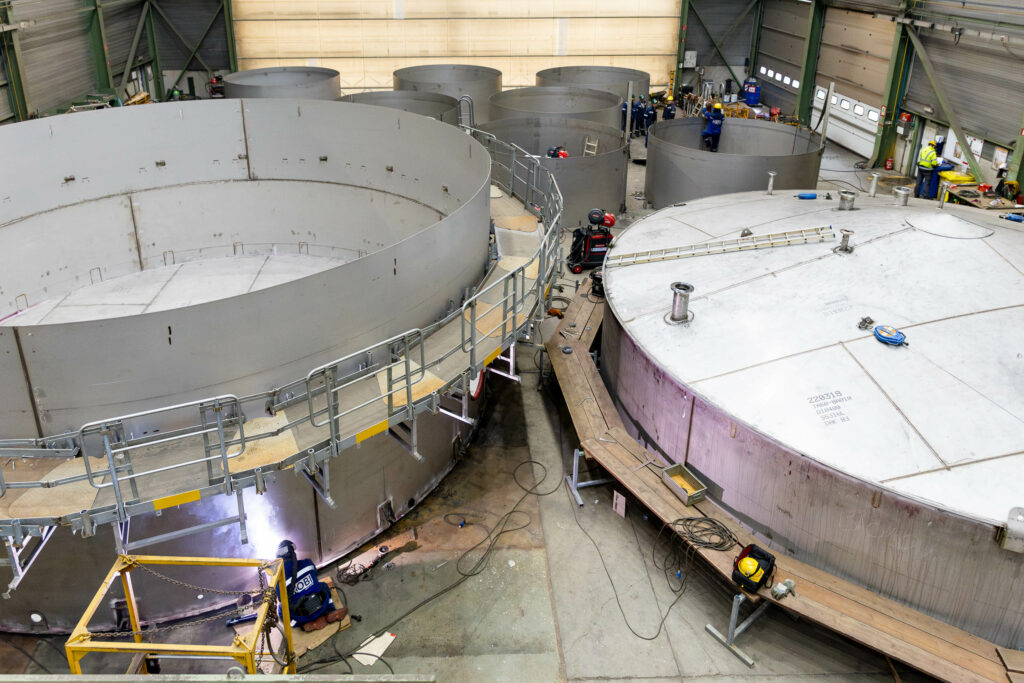
In the early days, Ivens mainly built storage tanks for the food industry and underground oil tanks. Since the rise of the petrochemical industry in the 1960s, the company mainly focuses on this market.
The tanks they build go up to 18 meters high and 50 metres in diameter. For that, they need high-quality cutting machines.
Ivens uses two plasma cutting machines from Wouters Cutting & Welding. One of 14 x 3 metres and one of 21 x 4,5 metres. But that last one has been renewed recently.
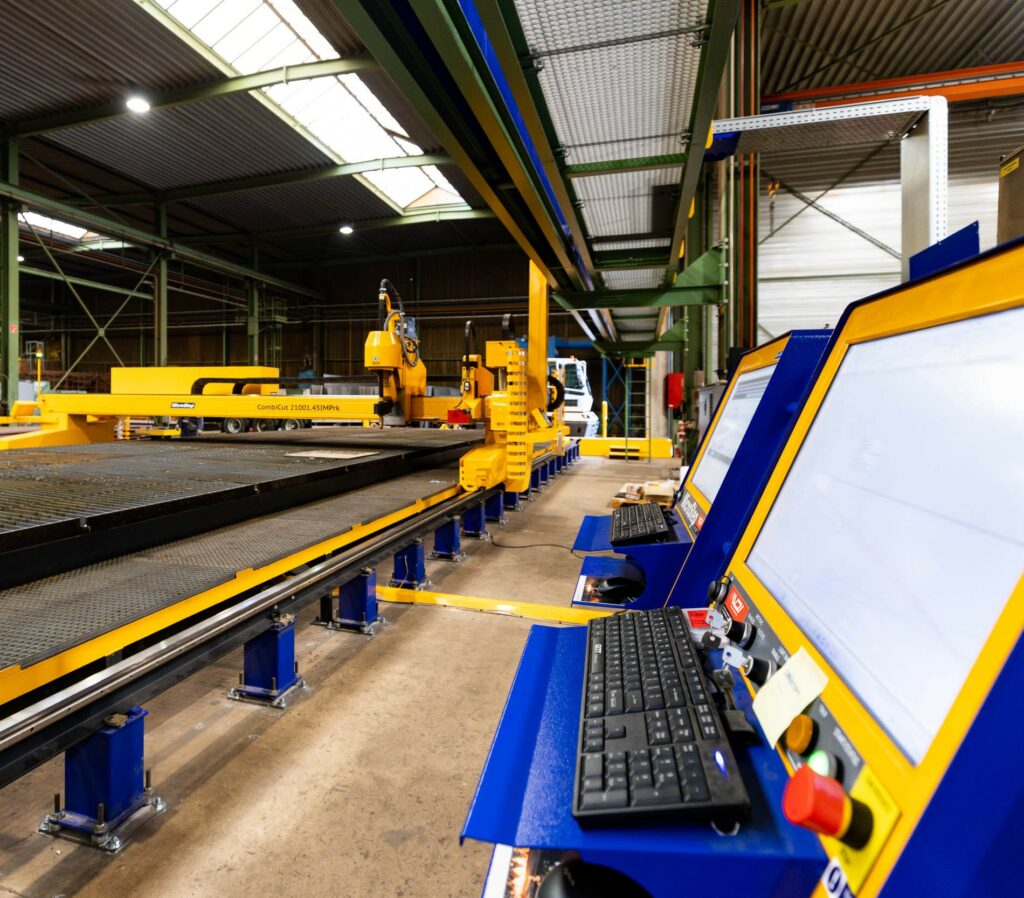
“After 14 years of intensive use, the machine needed to be replaced. We therefore contacted our trusted supplier, WCW, who recommended a CombiCut machine from Microstep,” says production manager Kris Luyten.
“Whereas the previous machine had a plasma source of 260 A, the new source has now been increased to 450 A. This means we can now cut plates up to 50 mm thickness.”
But cutting thick plates also requires precision. The plates must match exactly and they must have precise bolt holes.
“The cut remains perfectly straight thanks to Kjellberg’s ContourCut technology. Now we can make even more parts, such as lifting lugs, ourselves.”
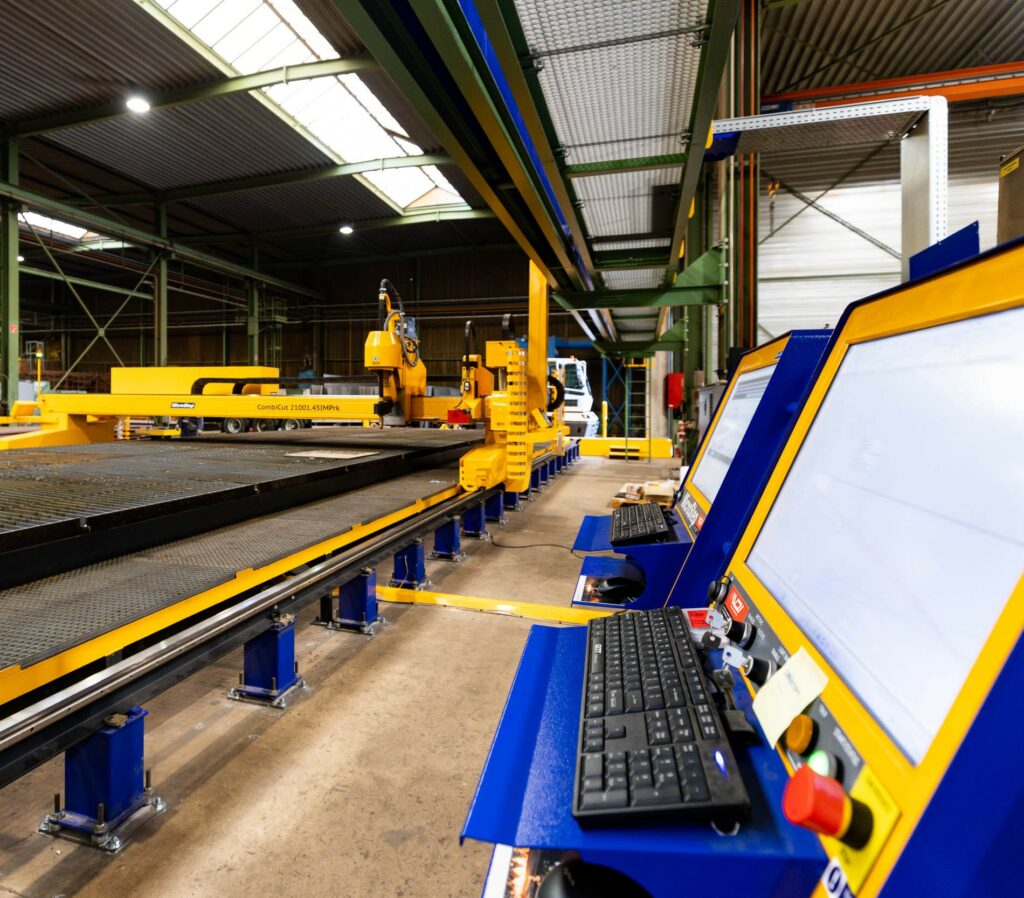
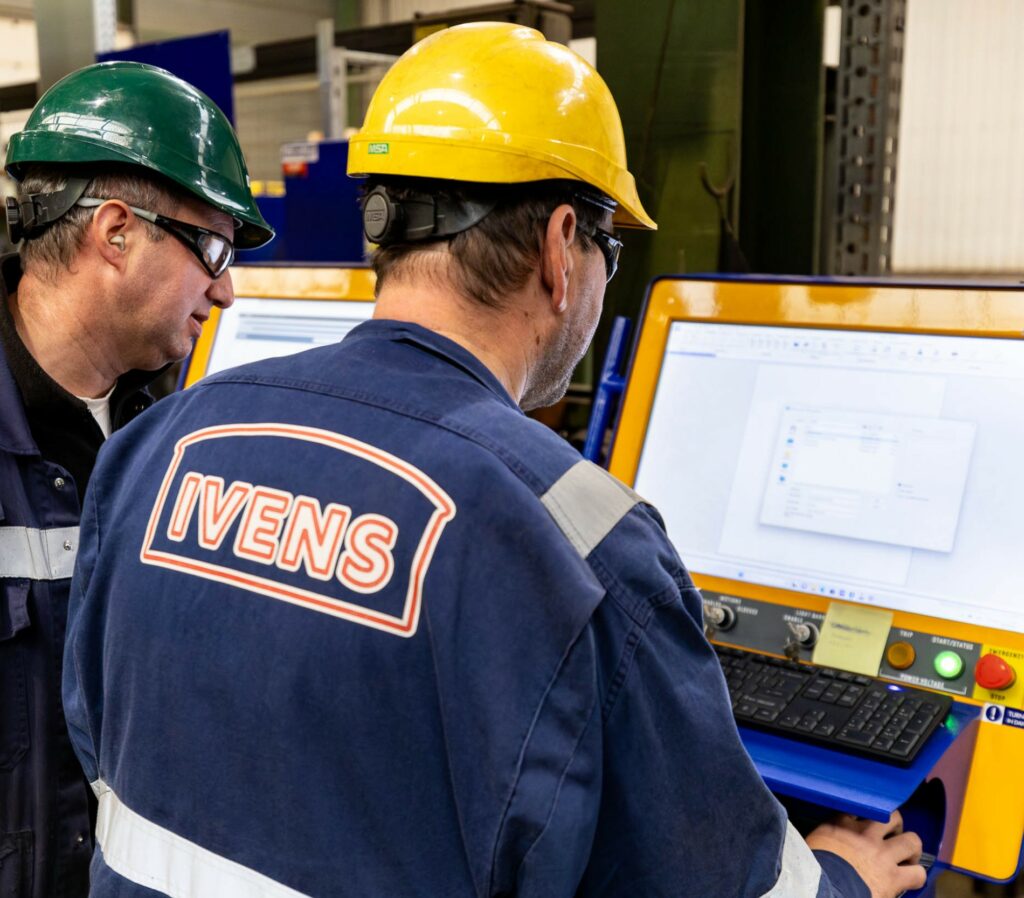
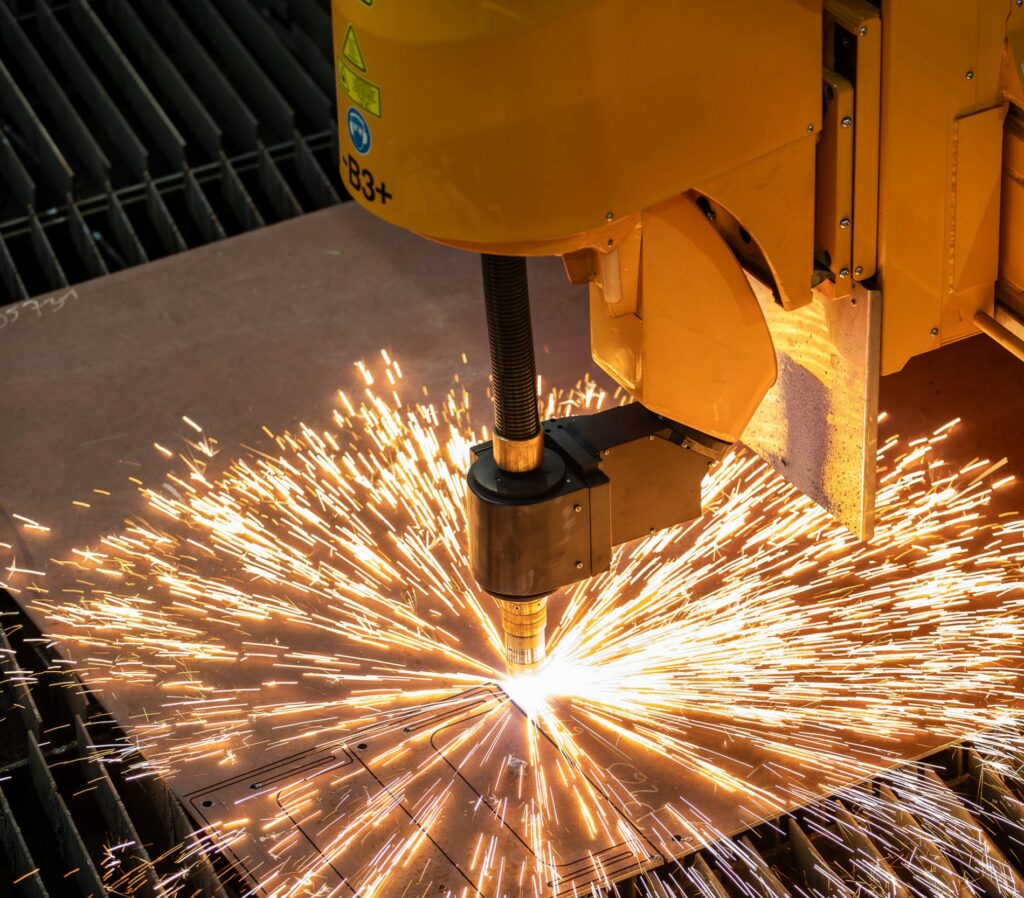
“The machine control has remained the same, which played a part in our choice for Wouters Cutting & Welding. This allows us to keep our employees working on both cutting machines, after a basic training.
But this wasn’t the only reason for choosing Wouters Welding & Cutting again .
“In case of any technical problems, we need to be up and running again as soon as possible. Wouters Cutting & Welding has already proven their added value here in the past in terms of maintenance and short response time, thanks to their experienced service technicians and proximity from Turnhout. As a distributor, they really make a difference for us with their short communication lines and easy accessibility in case of problems. Being both Flemish family businesses, we share the same values. You can definitely say we are a match.”
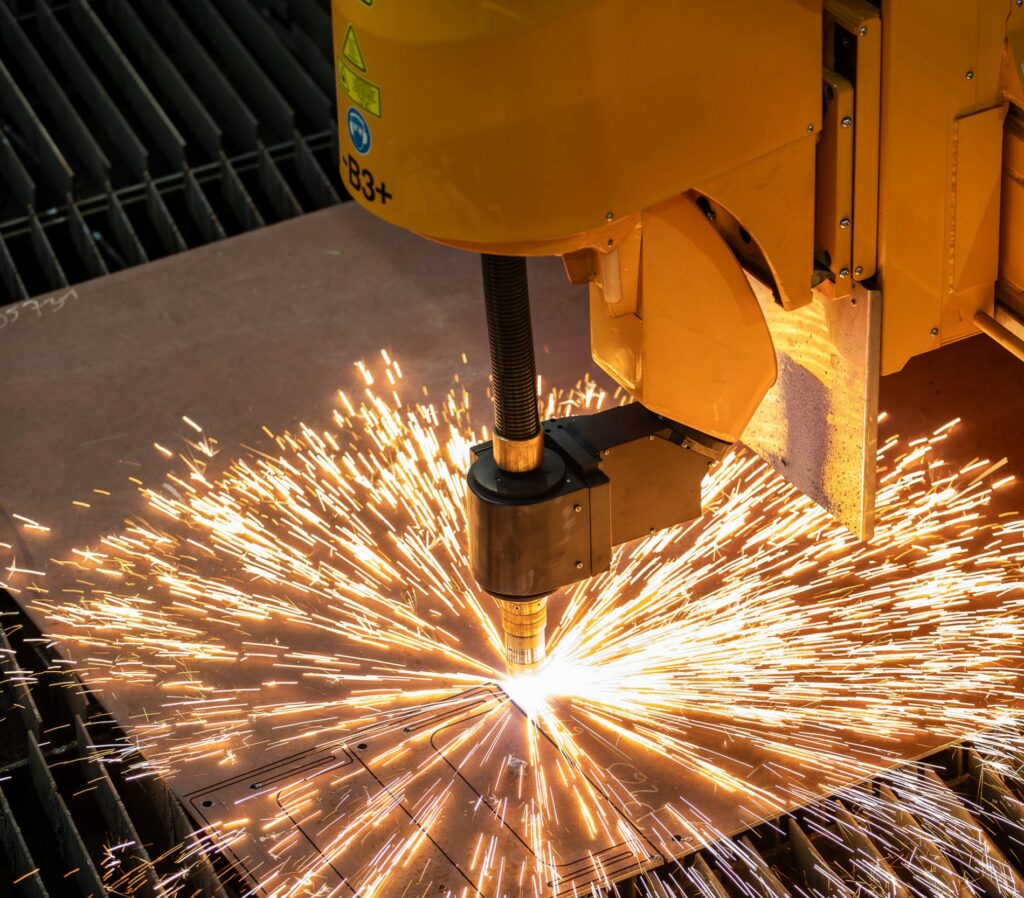
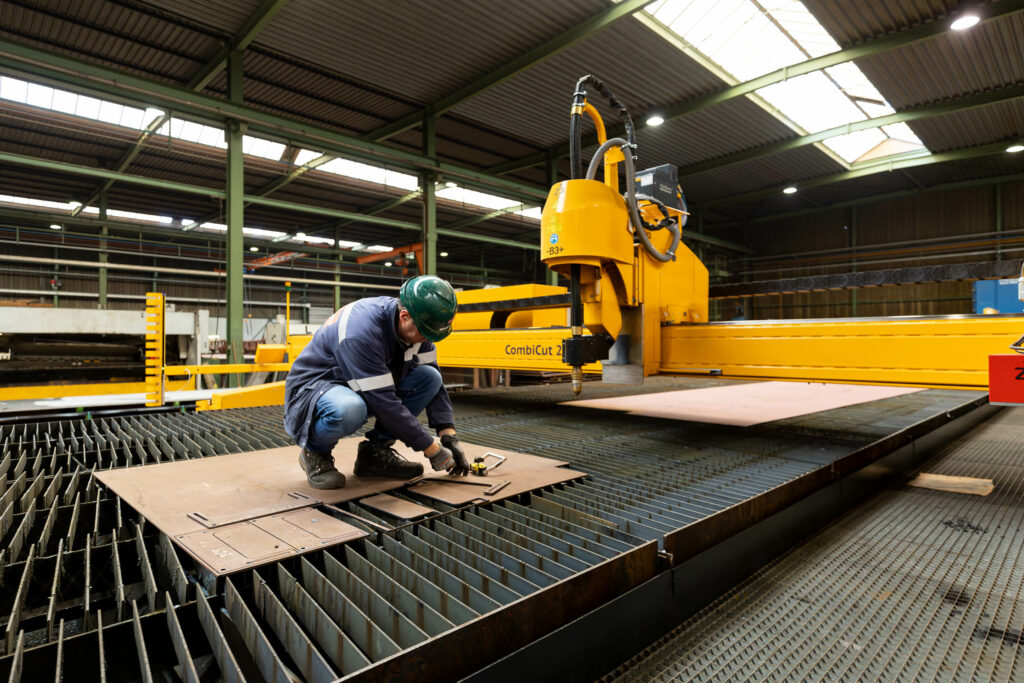
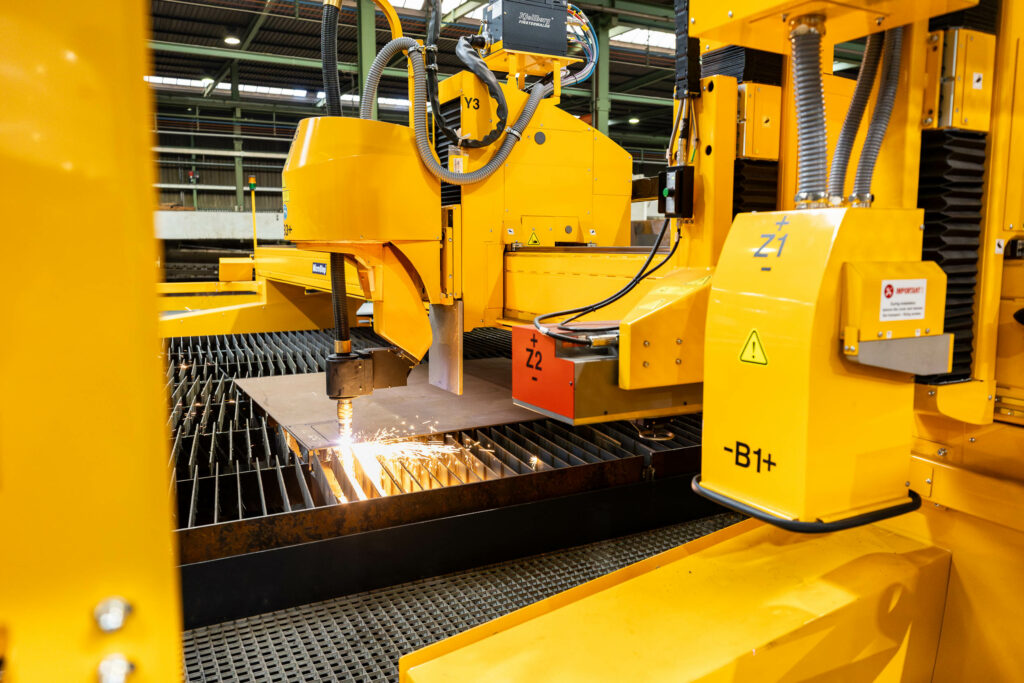
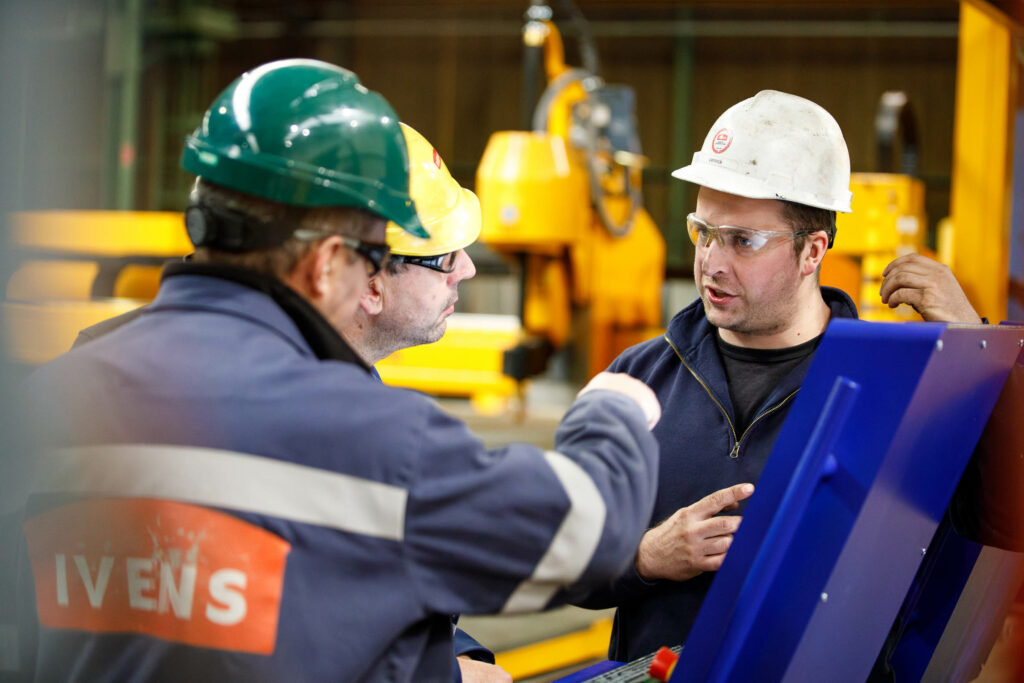
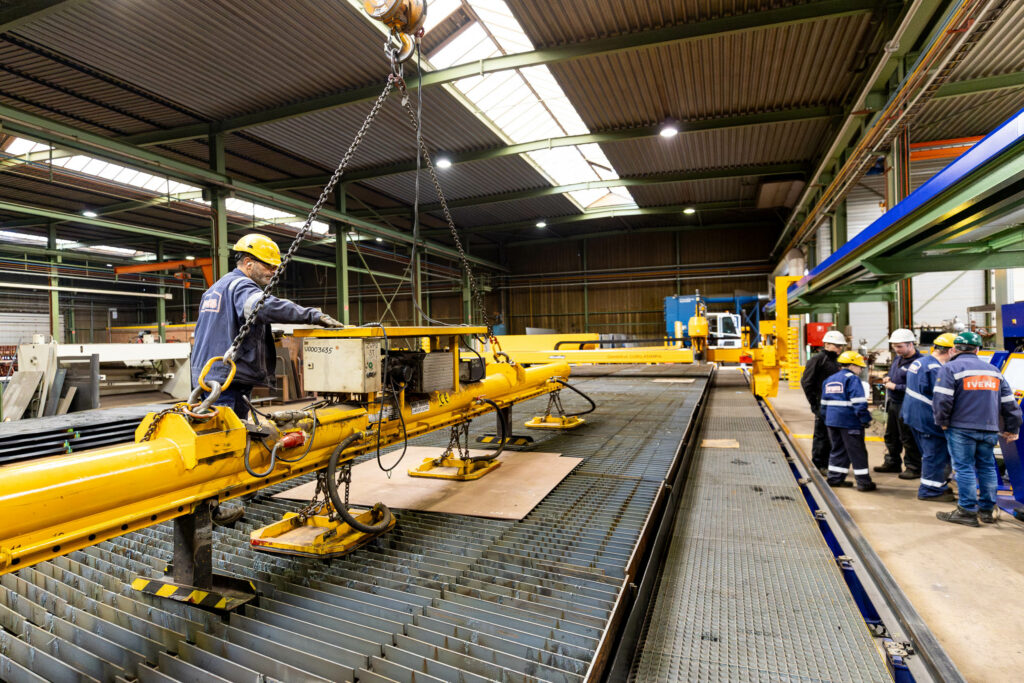
More cases
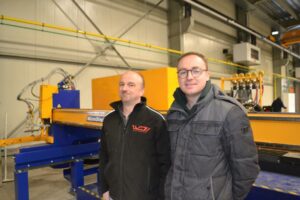
DEOM | MicroStep
Deom’s new MicroStep MasterCut combines high cutting accuracy with speed and automation.
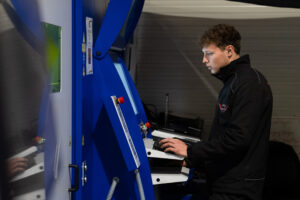
Snijtech | MicroStep
The new MicroStep laser cutting machine at Snijtech makes all the difference for them with its unique bevel control.
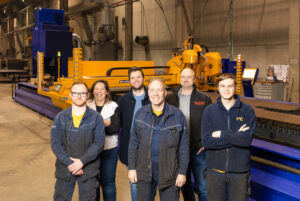
HYE | MG
With the new MicroStep MG, HYE is working more efficiently, flexibly and competitively than ever before.
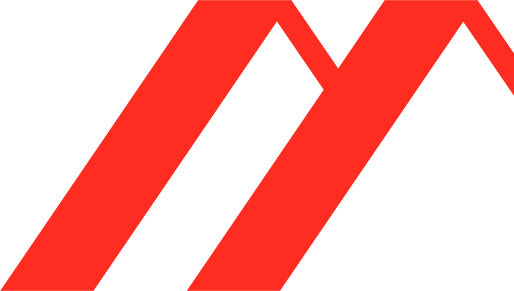
Looking for a cutting or welding solution?
Demo in our showroom or no-obligation appointment?
Or call us +32 3 475 98 25