Frequently asked questions
FIND YOUR ANSWER TO THE MOST FREQUENTLY ASKED QUESTIONS
Affordable, easy to use and yet with outstanding cutting quality. A Swift-Cut machine has it all. At WCW, you can choose between the plasma cutting machine and the waterjet cutting machine. Do you still have questions about one of the machines? Find the answer below or contact us!
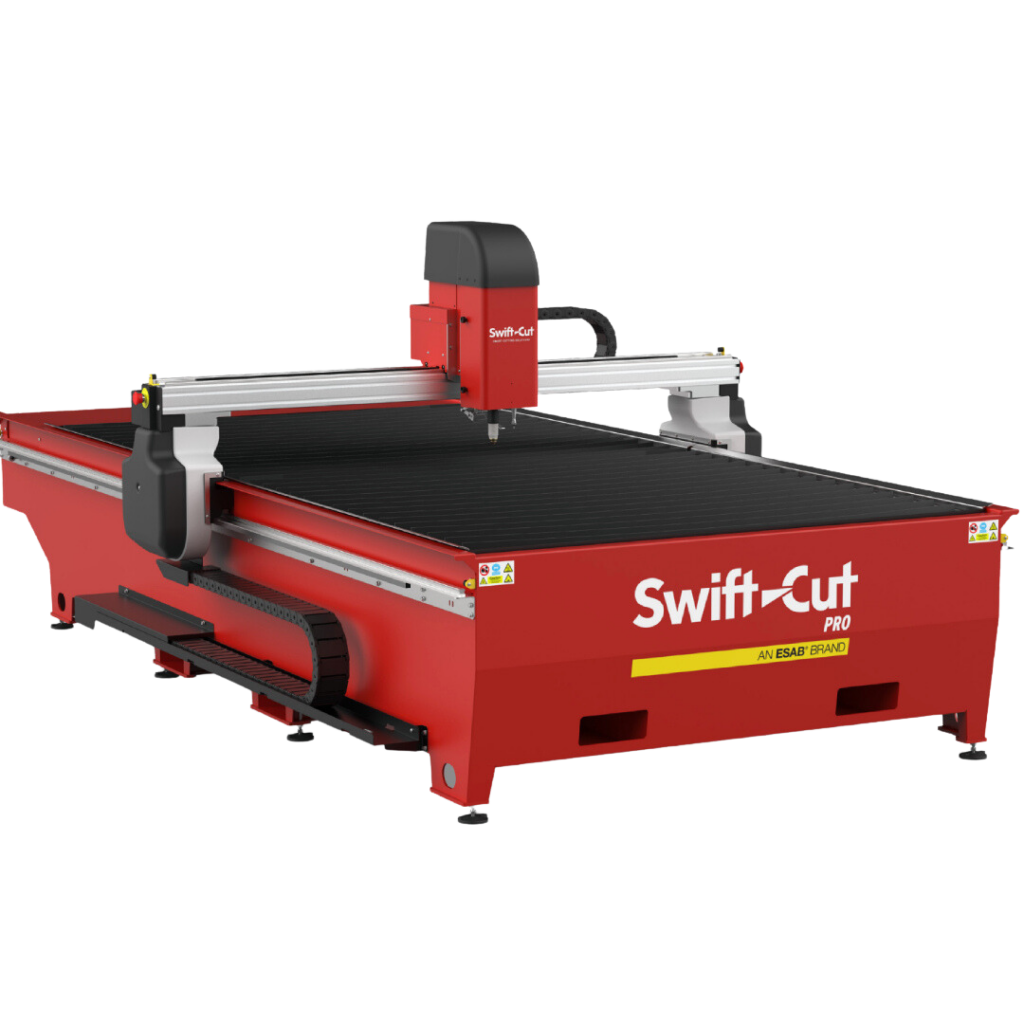
The Swift-Cut Pro and XP
The Swift-Cut Pro and XP are advanced cutting machines that use plasma technology to accurately and efficiently cut through a variety of materials. With their innovative features and intuitive operation, the Swift-Cut Pro and XP are the ideal solution for both small workshops and large industrial applications, upgrading cutting operations.
Below you can find a list of frequently asked questions. Still have any questions? Get in touch with an expert!
That depends on several factors. You have to take several things into consideration: the air quality, the material and the number of piercings. Is your machine set up correctly and are you using clean materials? Then consumables will last up to 1 to 3 hours.
An exception is the MaxPro 200 plasma source for the Swift-Cut XP. This source increases the lifespan of consumables (and therefore reduces costs) thanks to various technologies such as LongLife, CoolFlow™ and TrueFlow™.
The Pro and XP series machines are accurate to +/- 0.4 mm.
- CAM software → select sheet material and thickness
- CAM software → nesting
- CAM software → nesten
- CAM software → create CNC
- Machine → import CNC
- Machine → use the correct parts on the plasma source
- Machine → cut piece
You upload your DXF/DWG drawings into the SwiftCAM software from your own folders, network or USB stick. Uploading is very simple: you select the file and then click ‘import’. JPEG images are imported in the same way. After importing the images, you can then use the advanced image import function to clean up, scale or delete the drawing.
Once you have imported everything, follow the step-by-step process to nest your parts.
- Turn off the plasma source using the main switch.
- Unscrew the cartridge from the torch.
- Check and, if necessary, replace the cartridge with a new one.
- Turn the plasma source back on with the main switch.
There are many variables to take in consideration. You have to take in account the costs for power, compressed air, gases, cutting parts, the operator and routine maintenance. These variables make it difficult to put an exact rate on how much it costs to plasma cut.
Plasma cutting, compared to waterjet cutting, is cheaper, though.
The cost of plasma cutting compared to laser cutting depends on the thickness of the material. The thickness determines the cutting speed of your laser. With thinner materials, laser cutting is usually cheaper than plasma cutting.
Swift-Cut software is extremely user-friendly. Step by step, the software helps you nest your drawing or parametric shape and generate your CNC code. There are even different screen layouts to choose from depending on your knowledge and experience. This allows both beginners and experienced users to get started.
When you purchase a Swift-Cut cutting machine, you will always receive professional training on site.
Of course you can! You can see a demonstration of different cutting technologies and cutting machines at our site.
You can use any CAD programme on the Swift machines. As long as you can save the files in a DXF/DWG format, you can open them in the SwiftCAM software without any problems.
Swift-Cut plasma machines integrate seamlessly with Hypertherm plasma sources and torches. If you already have a Hypertherm plasma source, depending on its age, we can advise which parts are needed to connect it to one of our machines.
Yes. If you want to cut by hand, you need to disconnect the machine torch and CNC. Afterwards you can connect your hand torch. In addition, you need to put the material on the cutting bed of the Swift-Cut to make use of the mass. You can also connect a separate ground cable if you want to work without the Swift-Cut.
Have you finished cutting manually? Then you reconnect the machine torch and CNC.
No problem at all. We have many customers who cut profiles on our plasma cutting machines. The maximum height allowed on the machine is 100 mm for the Pro and 150 mm for the XP.
- When you cut very thin sheets, they will not be pressed down during the plate detection. This ensures the correct ignition and piercing height.
- When there’s a foil or primer on the plate, or when the plate is very dirty, correct plate detection can still be done.
When cutting holes with a standard single gas air plasma cutter, you can follow the 2xD rule. This means that your smallest hole should have a diameter twice the size of the material thickness. This way, you maintain good cutting quality and tolerance.
For example: when you have a sheet that’s 5 mm thick, the minimum diameter for cutting a hole will be 10 mm.
All our machines automatically calculate the best starting point, cutting height and cutting speed. This results in perfectly cut holes.
In the case of CNC plasma power sources, it’s best to look at its piercing capacity first. This is the maximum thickness you can cut with the plasma source. After that, you look at your own production. Which materials do I cut the most and need to be cut smoothly? 80% of the cutting power of your plasma power source should be large enough to cut those materials smoothly and qualitatively.
For example: you usually cut sheets with a thickness of 40 mm. In that case, you need a cutting power of 50 mm.
This ensures that your parts wear out less quickly and that your cuts are of a higher quality.
The power supply of your plasma cutter is determined by the maximum power of your chosen plasma source. Depending on how you configure your machine, we will be happy to advise you on the needed power supply.
Plasma is used only for conductive materials. The three most popular ones are mild steel, stainless steel and aluminium. But you can also cut copper, brass, titanium, Hardox, Inconel and cast iron with plasma.
All consumables can be purchased at WCW.
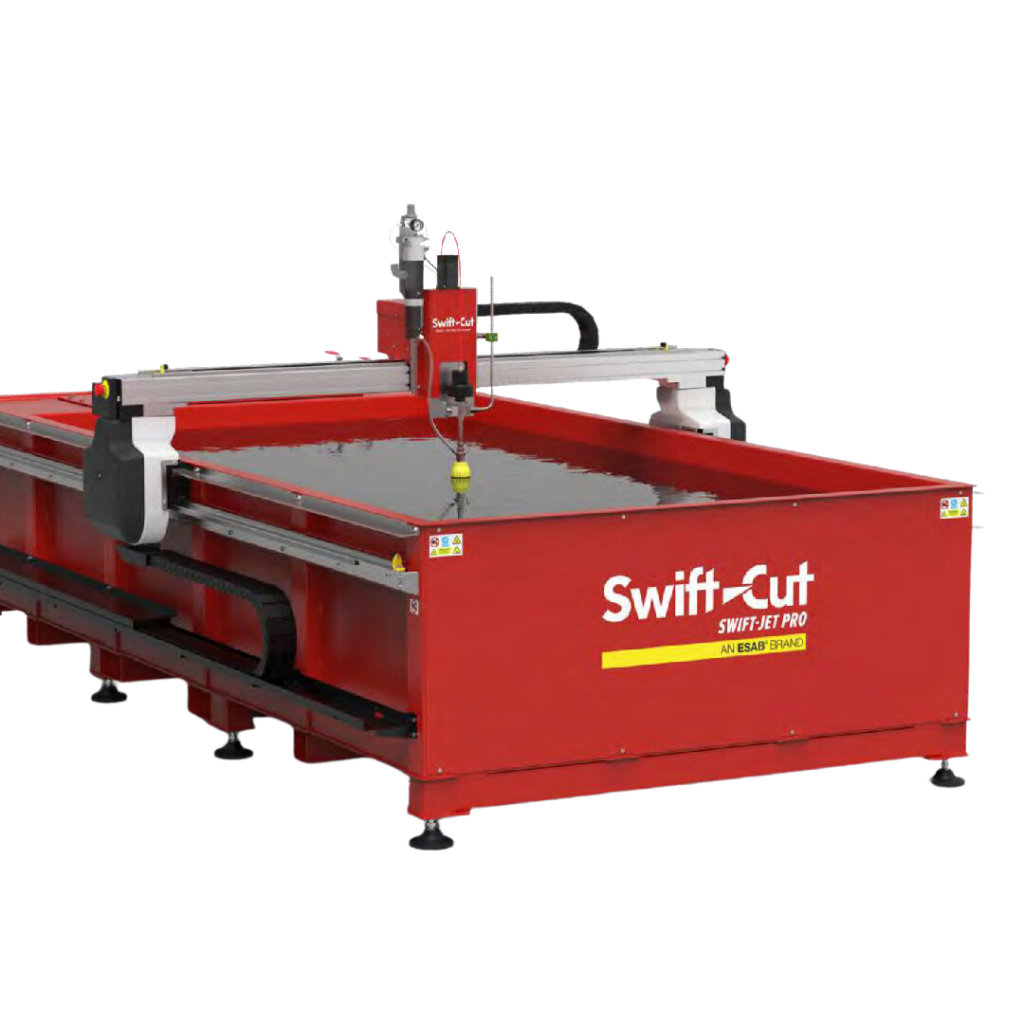
Swift-Jet Pro
The Swift-Jet Pro is perhaps the most versatile CNC cutting machine on the market. It cuts through almost any material thanks to the water jet mixed with abrasive. Heavy materials are very easy to cut. And the result? A smooth edge finish, no heat-affected areas and virtually no post-processing.
Below you can find a list of frequently asked questions. Still have any questions? Get in touch with an expert!
There are no guarantees for the life span of the consumables, but you can assume there are about 15 – 20 hours for a robein orifice, and about 30 – 40 hours for a nozzle (when using the required cutting water quality).
The abrasive should be stored dry and away from humid environments.
Waterjet cutting of metals is a relatively slow process, but as with all cutting processes, the speed depends on the type of material and its thickness, the power of your pump and the cutting quality that is required.
The Swift-Jet Pro table can cut up to 10 m/min through soft materials such as foam, but for 25 mm granite, for example, the speed is more likely to be 25 mm/min.
That depends on the system you are using. Water jet machines have always been expensive to purchase and use. The Swift-Jet Pro was designed to break that trend.
To do so, Swift-Cut started from the successful Pro plasma table design. After some specific upgrades to the drive and gantry, the design maintains an incredible value for money.
But there’s more. The direct-drive high-pressure pump is 30% more efficient than intensifier pumps. The average cost (abrasive, water, power, consumables…) is therefore much lower compared to other waterjet systems.
Swift-Cut is known for combining user-friendliness with comprehensive features. The Swift-Jet Pro is no exception. In fact, customer feedback shows that many users could not believe how much the machine is able to do without involving complex systems.
Still have questions? There’s always a technical support engineer ready for you at WCW.
Yes. You can purchase abrasive from WCW at any time.
Silent waterjet cutting does not yet exist. You are cutting with abrasive and more than 3,000 bar (or 43,000 psi), and that involves noise.
But you can reduce the noise. That’s where our adjustable water level system comes in, combined with a low-speed direct-drive pump.
Technically, you can reuse cutting abrasive, but in reality this happens very rarely. Swift-Cut does not offer a product or service to reuse cutting abrasive, but there are companies that can help you with this.
Be careful, though, and do this with caution. New abrasive has a certain sharpness & grain size and has properties that are different from used abrasive.
Used abrasive can slow down cutting speeds, cause irregular flow or even damage your workpiece.
If the abrasive runs out, the Swift-Jet Pro immediately stops cutting. In such a case, you refill the reservoir and continue where you left off. No hassle, no waste of material.
Does your Swift-Jet Pro detect a drop in water pressure? If so, the machine will automatically stop cutting and an error message will appear on the screen. Locate the problem and restart the water supply. Finally, use the ‘restore cut’ function to start your cut exactly where you finished.
All the cutting abrasive is released into the cutting table, after which it sinks to the bottom. To remove the abrasive, you will need a special removal system (aftermarket options are available) or you can do it manually.
The abrasive is not dangerous, nor are the materials you cut with your Swift-Jet.
We do recommend emptying your tank for every two tonnes of abrasive used.
For the Swift-Jet machine, you need a single-phase power supply (230V / 6A). For the high-pressure water pump, you need a triple-phase power supply (380V / 40A).
The table’s linear positional accuracy is 0.2mm/m and its repeatability is 0.4mm/m. Do you have a particular piece in mind? Then contact us and we will be happy to make a sample part.