Plasma cutting
Plasma cutting is a versatile technology for cutting sheet metal, profiles, tubes and pipes. This technique is therefore frequently used for parts that are subsequently welded, such as metal construction, shipbuilding and offshore companies. Plasma cutting is also a common alternative for materials where gass cutting is less or not suitable, such as aluminum and stainless steel. In addition, the cutting speed of plasma is many times faster than that of oxyfuel cutting.
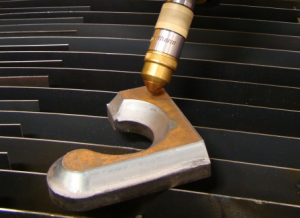
Advantages of plasma cutting
- Suitable for steel, stainless steel, and aluminum, as well as other electrically conductive materials
- Smooth cutting speed
- Possibility to cut a welding edge preparation (bevel cutting)
- Suitable for a wide range of sheet thicknesses, depending on the plasma source
- Possibility to cut holes with a minimum diameter equal to the material thickness
MicroStep plasma cutting machines
For high end solutions and heavy production applications, we rely on our MicroStep plasma and oxyfuel cutting machines.
Swift-Cut plasma cutting machines
Swift-Cut has made it their mission to produce quality machines with a high cutting speed and user-friendly software at a low investment cost. The Swift-Cut plasma cutting machines are therefore the ideal solution for schools, training centers and maintenance and construction companies.
Oxyfuel cutting
Oxyfuel cutting is a relatively simple cutting process, in which an active gas together with oxygen forms a flame and burns away the material. Because of its simplicity, this technology was often chosen in the past. Now we recommend oxyfuel cutting mainly in combination with plasma cutting, because the speed of plasma cutting is many times faster, but oxyfuel cutting can handle higher cutting thicknesses. In addition, a cutting machine solely equipped with oxyfuel technology can be the suitable solution for companies that only cut very thick material.
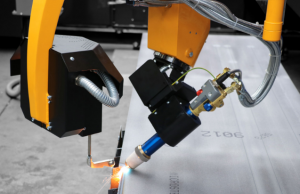
Benefits of oxyfuel cutting
- Very simple cutting process
- Low investment
- Suitable for steel up to a thickness of 300 mm, or thicker in special applications
- Possibility to cut a welding edge preparation (bevel cutting)
MicroStep oxyfuel cutting machines
We rely on our MicroStep plasma and oxyfuel cutting machines for our high end solutions and heavy production applications.
Waterjet cutting
In waterjet cutting, water is forced through the cutting head at an extremely high pressure, reaching a speed of approximately twice the speed of sound. The impact energy of the water on the material to be cut creates a clean thin cut. This makes waterjet cutting the ideal solution for very precise cutting. Thin or soft material can be cut with just water. An abrasive (sand) is added to cut thicker or harder material.
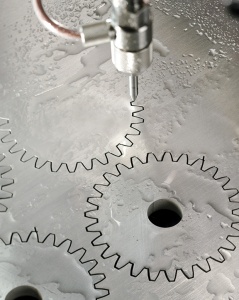
Advantages of waterjet cutting
- Suitable for almost all homogeneous materials
- High precision and dimensional accuracy
- No heat affected zone
- High quality cutting edge
MicroStep waterjet cutting machines
We rely on our MicroStep waterjet cutting machines for our high end solutions and heavy production applications.
Swift-Jet cutting machine
Swift-Cut has made it their mission to produce quality machines with a high cutting speed and user-friendly software at a low investment cost. The Swift-Jet cutting machine is therefore the ideal solution for schools, training centers and maintenance and construction companies.
Laser cutting
Due to its great freedom of shape and high quality, laser cutting is one of the most common used industrial cutting technology. With this technology, a bundled light source is focused on the material, which results in heat that melts the material, after which it is blown away by oxygen or nitrogen.
The choice for a laser cutter is often determined by the required cutting quality. The intensity of the light beam allows to cut with extreme precision, so that in most cases no finishing is required. In addition, the cutting speed of laser cutting is very high, making it the ideal solution for companies where high productivity is key.
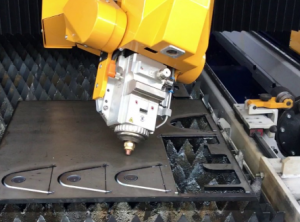
Advantages of laser cutting
- Suitable for a wide range of metals and non-metals
- High cutting speed
- High precision and dimensional accuracy
- High quality cutting edge
- Small heat affected zone and therefore minimal thermal deformation of the product
- Ability to cut complex contours
MicroStep laser cutting machines
For laser cutting, we rely on the technology of the MicroStep MSF series of fiber laser cutting machines.
First of all there is the MSF Compact, which makes it possible to laser cut limited dimensions (up to 3 meters) in a cost-efficient manner. Those who work with larger dimensions can rely on the standard MSF Pro and the MSF-Max for extreme dimensions.
In addition to plate and pipe cutting, this MSF series can also uniquely be extended with the bevel cutting option.
Welding solutions
In addition to cutting machines, we have a wide range of solutions for both manual and automatic welding.
For manual welding, we advise you in the various welding equipment and consumables from Lindoln Electric.
For welding automation, we count on the technology of Pema from Finland, for which we are the Benelux dealer. Curious about how welding and production automation can help your business grow? We are happy to advise and guide you in your next project.
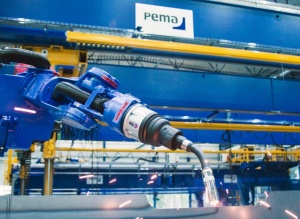
Filter technology - Fume extraction
In combination with our cutting and welding solutions, we also offer various solutions for efficient extraction of welding and cutting fumes.
For filtering at CNC cutting machines, we work together wit Donaldson Europe. The compact DFPRO series and versatile DFO series are our most commonly used solutions. They guarantee a long life for your filters and filter cartridges.
Additionally we also provide solutions for welding fume extraction. For as well as mobile applications as stationary filters with extraction arms and compact welding fume extraction tables, we rely on Lincoln Electric’s filter technology.
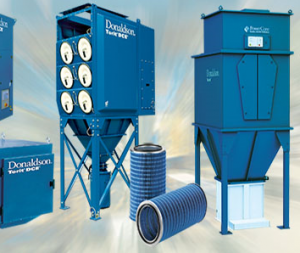