CASE
Jan De Nul Group
“Now everything happens in one step, resulting in huge time savings”

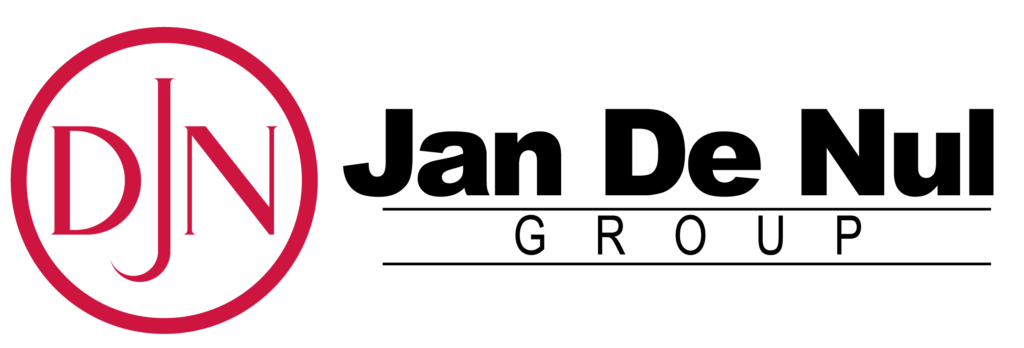
About Jan De Nul Group
Does Jan De Nul Group even need an introduction? This giant is one of the largest dredging companies in the world, a reputation they have built since their founding in 1938. Their most famous projects are undoubtedly the Palm Islands in Dubai and the dredging of the Suez Canal.
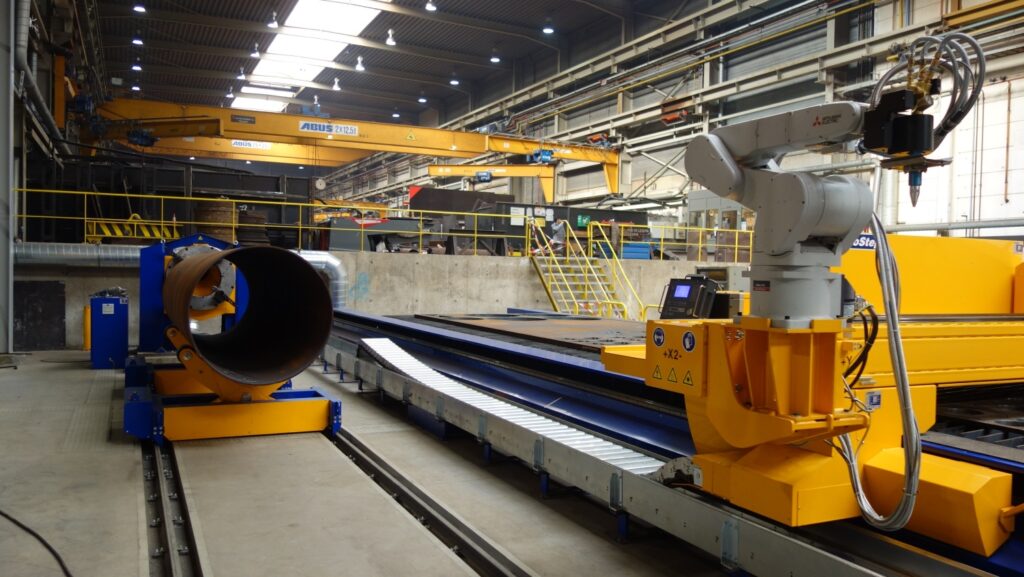
To successfully complete these projects, Jan De Nul Group relies on its own fleet, consisting of no less than 85 ships, some of which are among the largest and most powerful in the world.
They design and build all of these ships themselves, making them one of the only dredging companies in the world to do so.
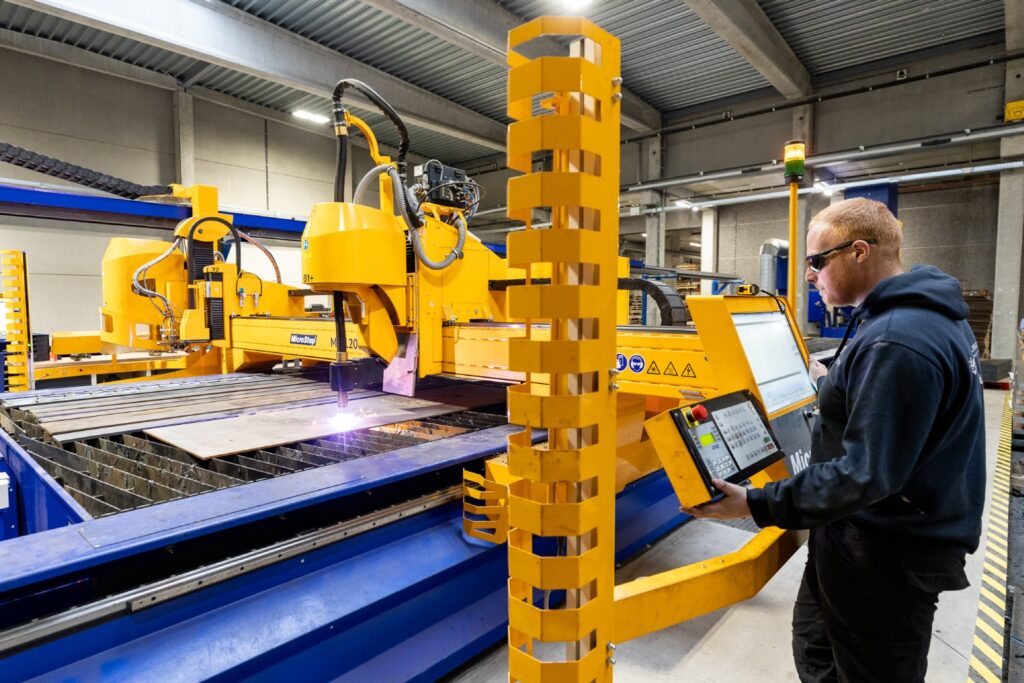
“Firstly, this allows us to have better control over delivery times. Then there’s the matter of quality. Often, these are quite complex parts with irregular shapes that require a lot of know-how. We believe that we can still produce these mostly complex parts best ourselves. Moreover, this is expertise we prefer to keep in-house rather than outsource,” explains José Pycke, Workshop Manager at Jan De Nul Group.
Recently, however, Jan De Nul Group encountered an inefficiency in the production process. To address this, they turned to Wouters Cutting & Welding for a new plasma cutting machine. Their choice ultimately fell on the MG from MicroStep.
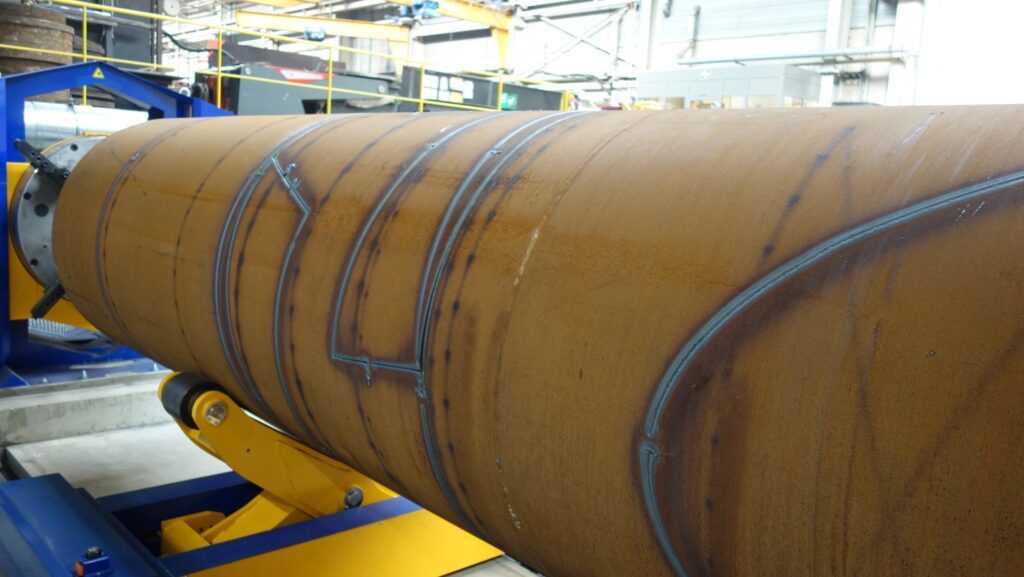
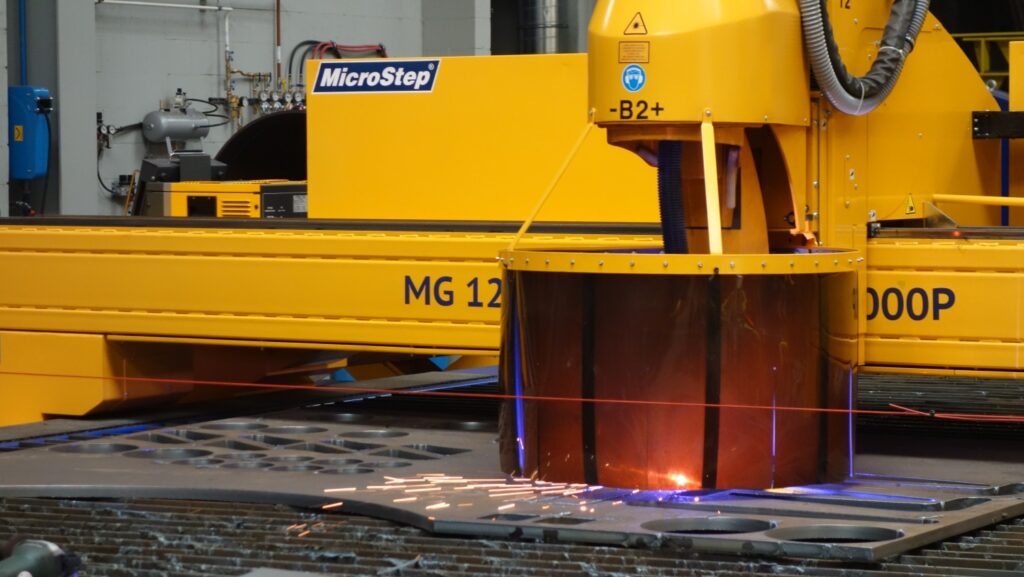
“Our old flame-cutting machine was still working, but it couldn’t cut weld bevels. These had to be added manually after the (straight) cut, using a cutting torch or an angle grinder, which took a lot of time. The MicroStep machine has put an end to that,” says José Pycke.
The CNC control of the MG automatically generates the program. Additionally, it is equipped with a rotating cutting head with an angle range from -50° to +50°. This cutting head has built-in safety, ensuring that all weld seams are cut with precision. Add to that the Kjellberg ContourCut and bevel correction, and you know Jan De Nul Group has an exceptional cutting machine.
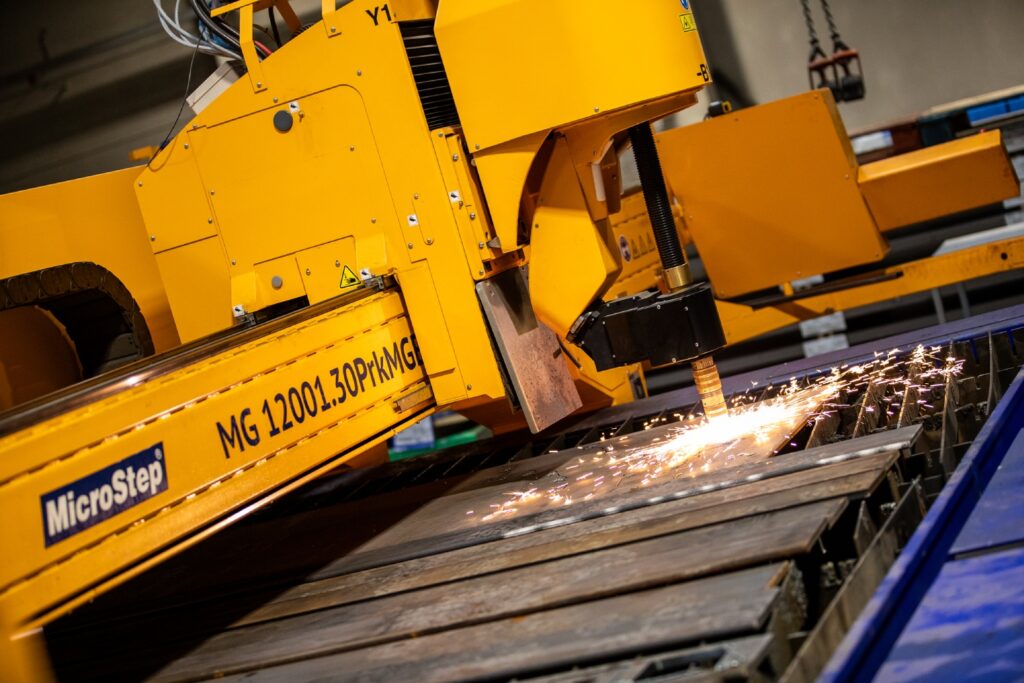
The machine is also more powerful. The plasma source has been increased to 440 A, raising the cutting capacity from 20 mm to a maximum of 50 mm plate thickness. Before the MG, they had to switch to slower oxy-fuel cutting starting at 25 mm thickness.
And why stop there?
With a MicroStep, you can go in many different directions. Jan De Nul Group was happy to take advantage of this opportunity. They installed a Mitsubishi robot on top of the machine to automatically cut pipes up to 2,000 mm in diameter and 80 mm thick.
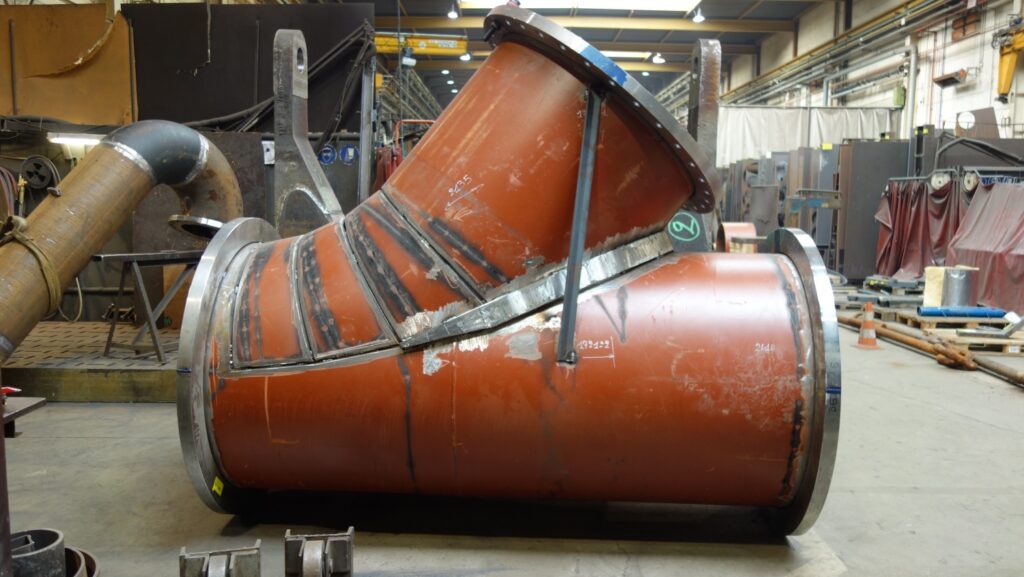
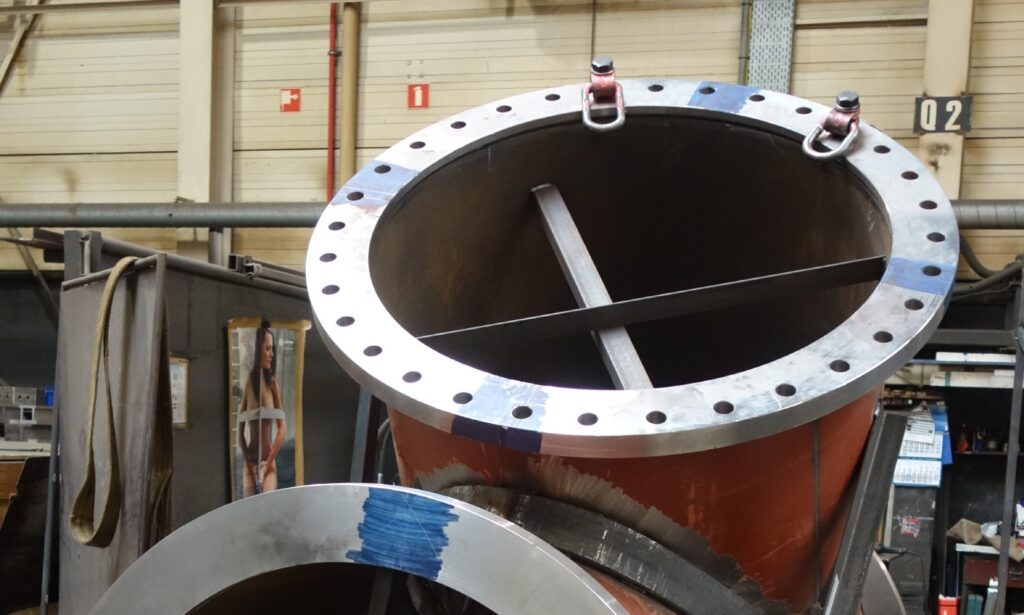
Was the client satisfied? Absolutely.
“The plasma and oxy-fuel cutting machine with an integrated robot has primarily resulted in significant time savings because all weld bevels are now automatically cut with the plasma rotating head in a single cutting step. As a result, quality has also improved. Regarding pipe cutting, our range has expanded, and we can now cut any shape. We have made great progress in terms of flexibility,” concludes Pycke.
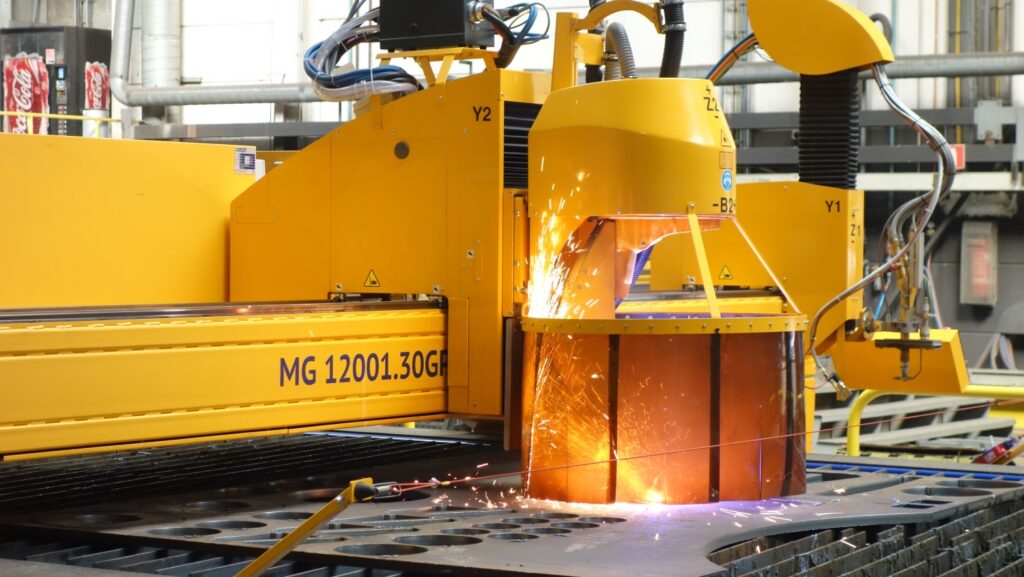
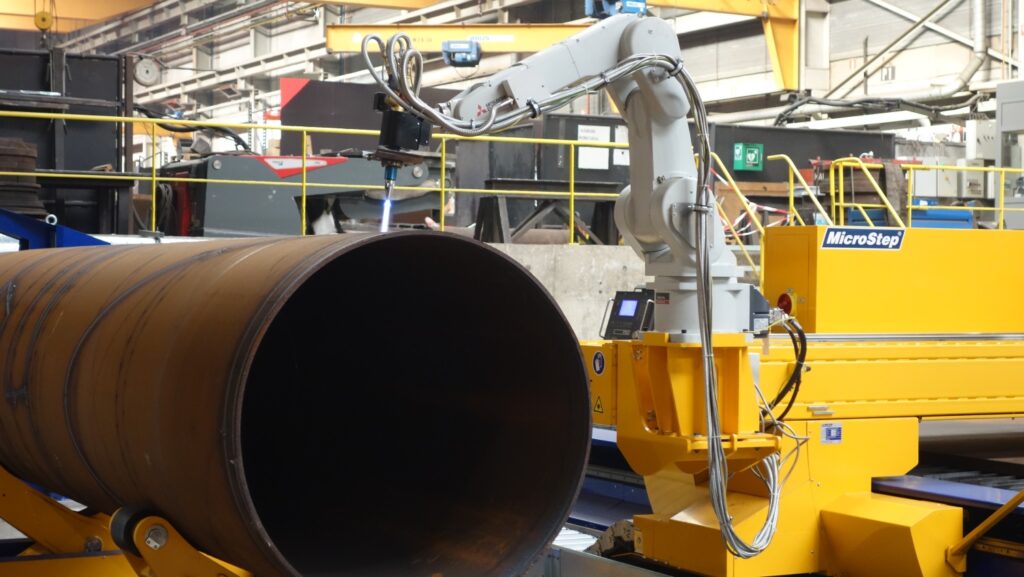
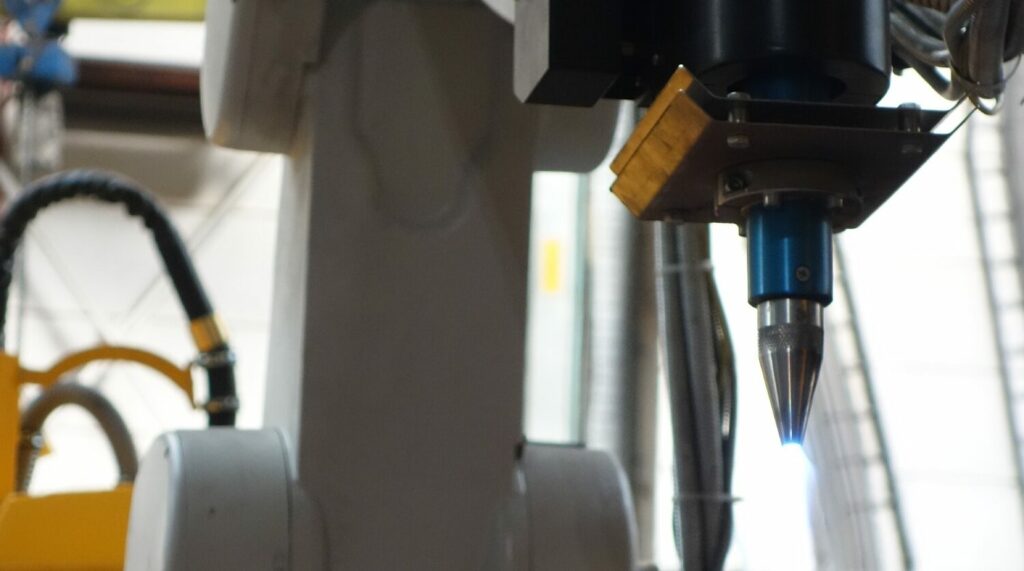
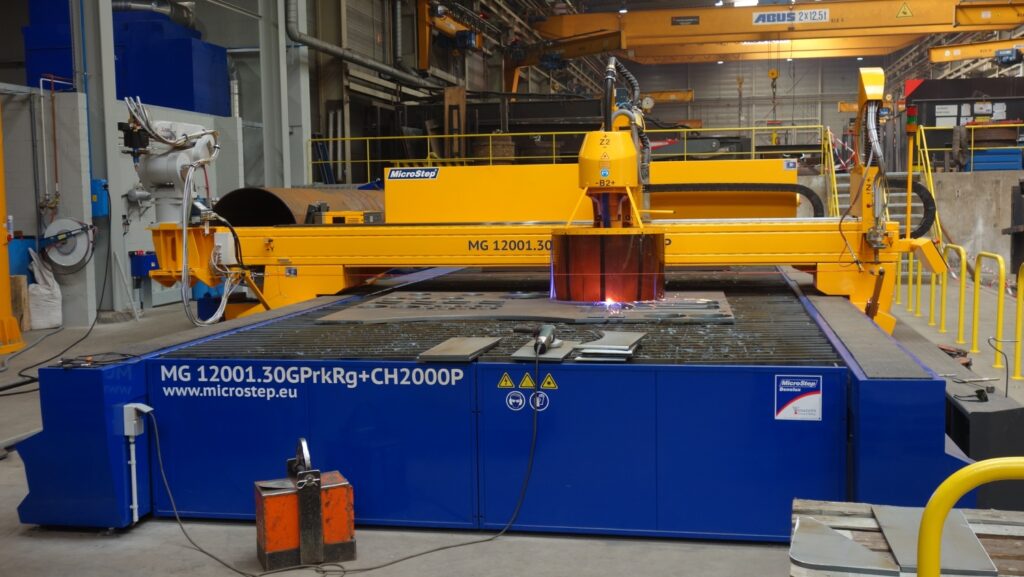
More cases
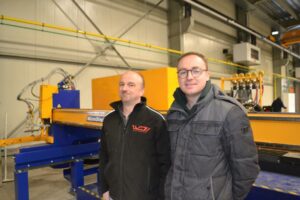
DEOM | MicroStep
Deom’s new MicroStep MasterCut combines high cutting accuracy with speed and automation.
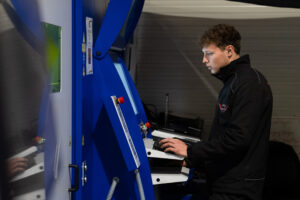
Snijtech | MicroStep
The new MicroStep laser cutting machine at Snijtech makes all the difference for them with its unique bevel control.
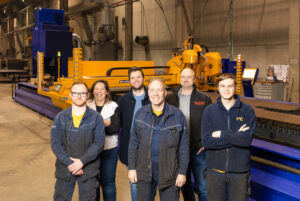
HYE | MG
With the new MicroStep MG, HYE is working more efficiently, flexibly and competitively than ever before.
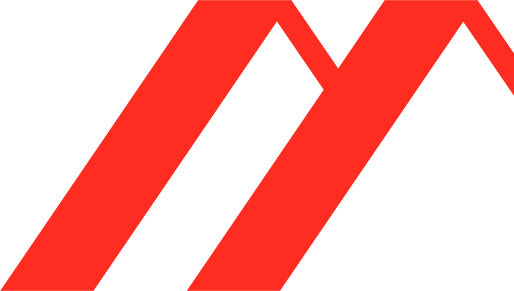
Looking for a cutting or laser machine?
Demo in our showroom or no-obligation appointment?
Or call us +32 3 475 98 25