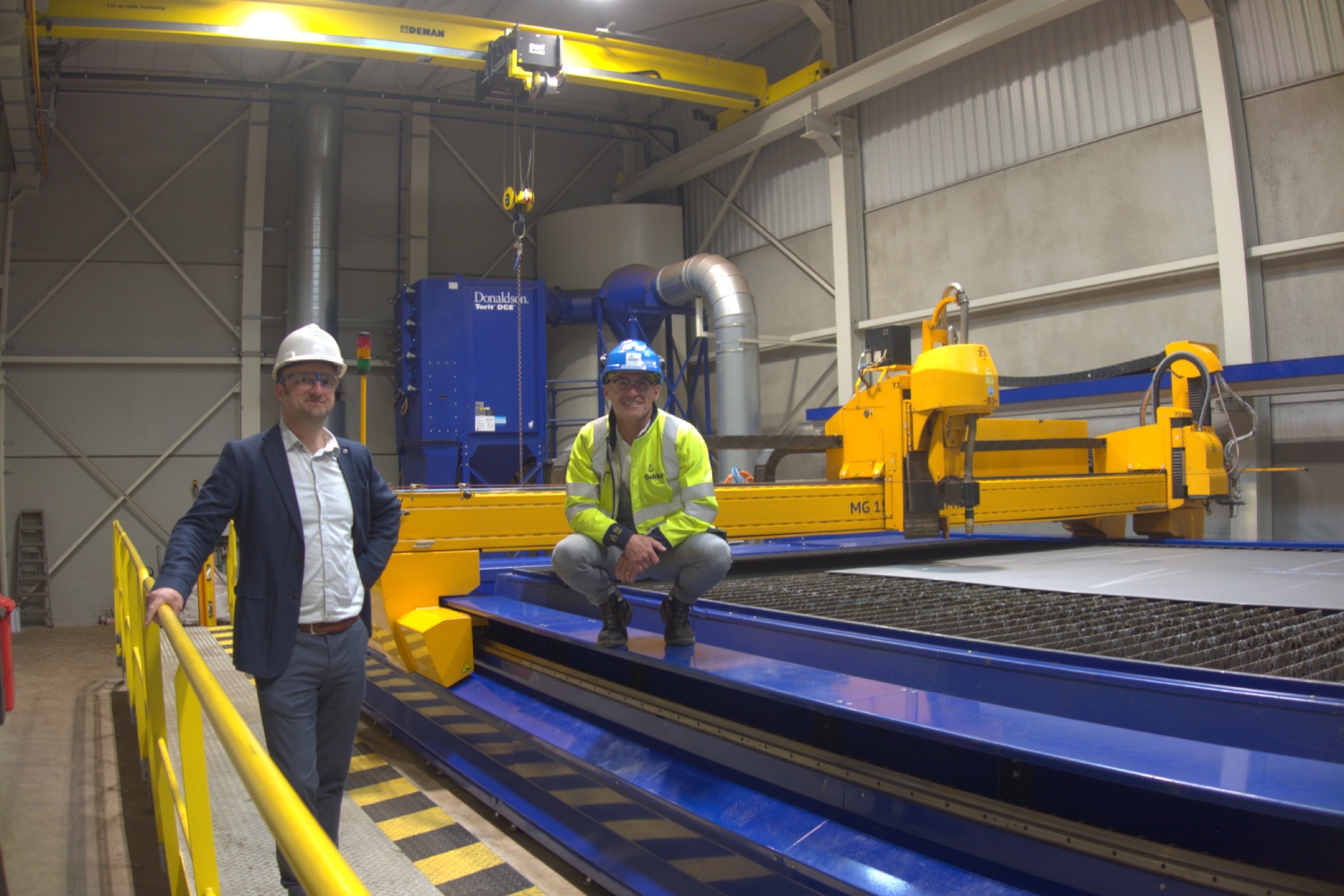
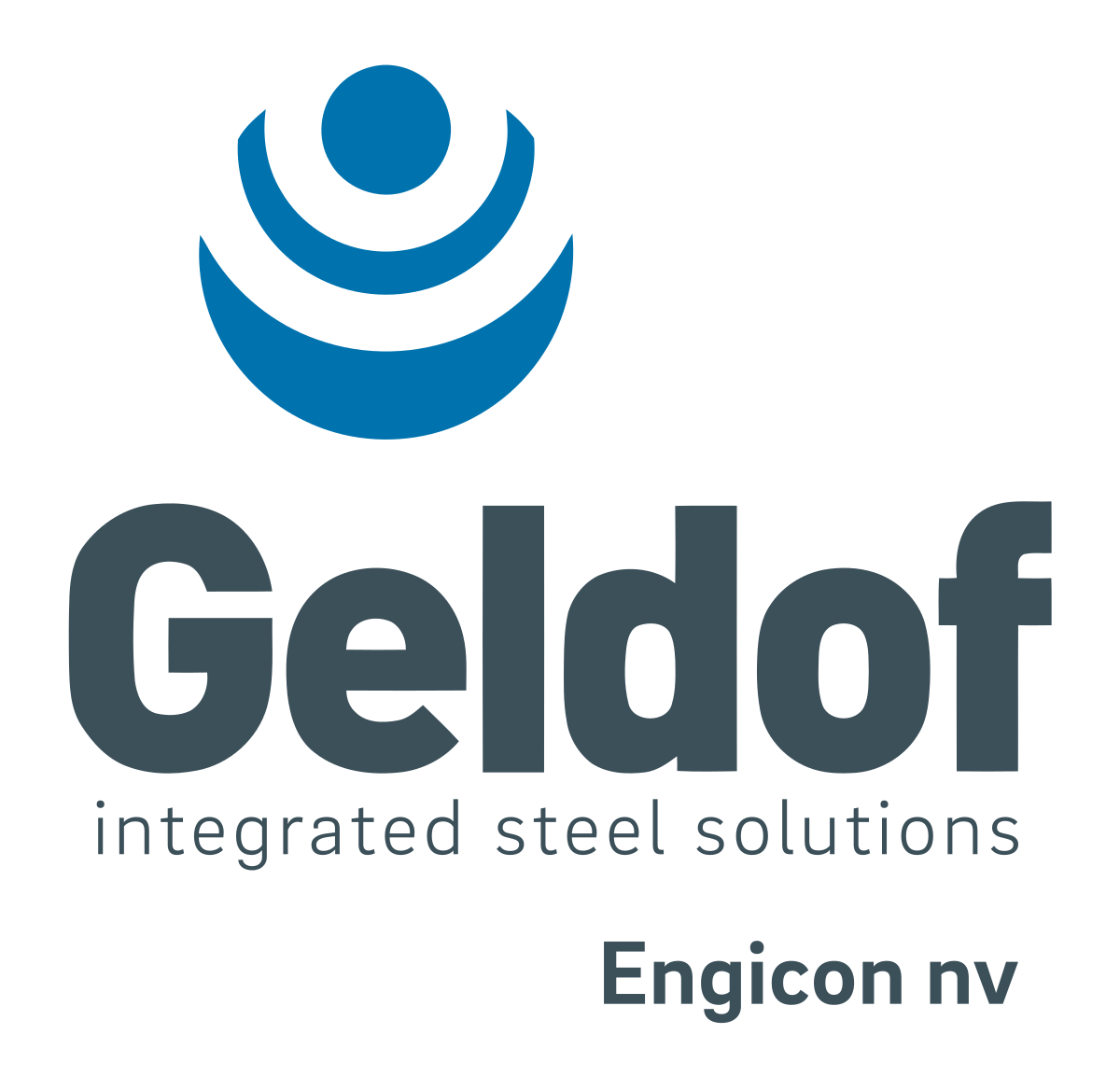
About Engicon (Geldof)
In 1969, Geldof Metal Construction was founded. In previous years, the company had been active in the flax industry, but it saw the future potential of the metalworking industry and thus shifted its focus.
Half a century later, it changed the company name to Engicon, a name that better aligns with its international ambitions. Today, it s an European leader in the construction of metal storage solutions.
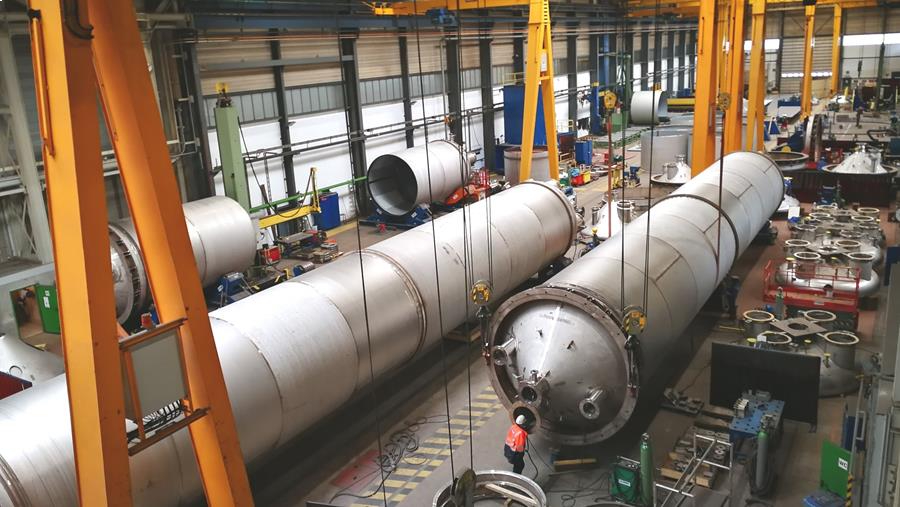
Recently, Engicon invested in a new plasma cutting machine and exchange table at Wouters Cutting & Welding. Dieter Vandeputte, facility manager at Geldof, explains.
“Our previous cutting machine was over 30 years old and could no longer provide the necessary capacity and quality. Furthermore, the availability of spare parts could no longer be guaranteed, so we decided to look for a new cutting machine. We briefly considered laser technology, but the thickness of most of our plates and the speed difference with plasma cutting machines ultimately led us to choose the latter.”
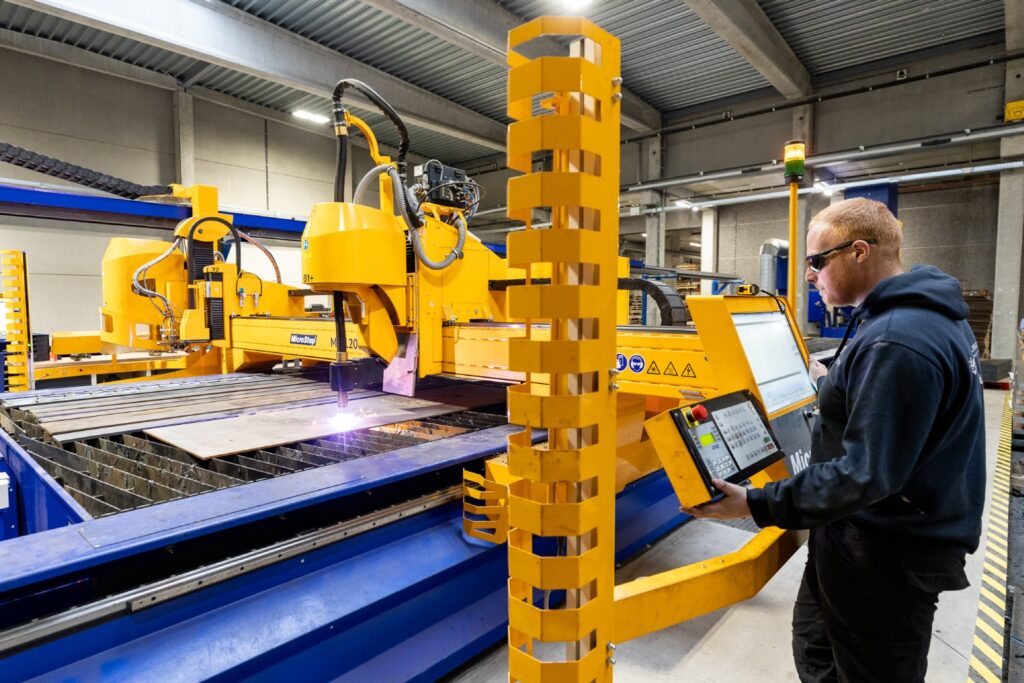
Eventually, they chose the MicroStep MG plasma cutting machine with a Tecloga POWERtrac exchange table.
The MicroStep opens up a world of new possibilities. Three cutting heads ensure a significant boost in Engicon’s productivity. And it doesn’t stop there.
“Whereas we previously could only cut straight contours and then had to bevel manually (or use a separate machine), this functionality is integrated into the new machine with a plasma rotary bevel head, saving us a lot of time,” says Vandeputte.
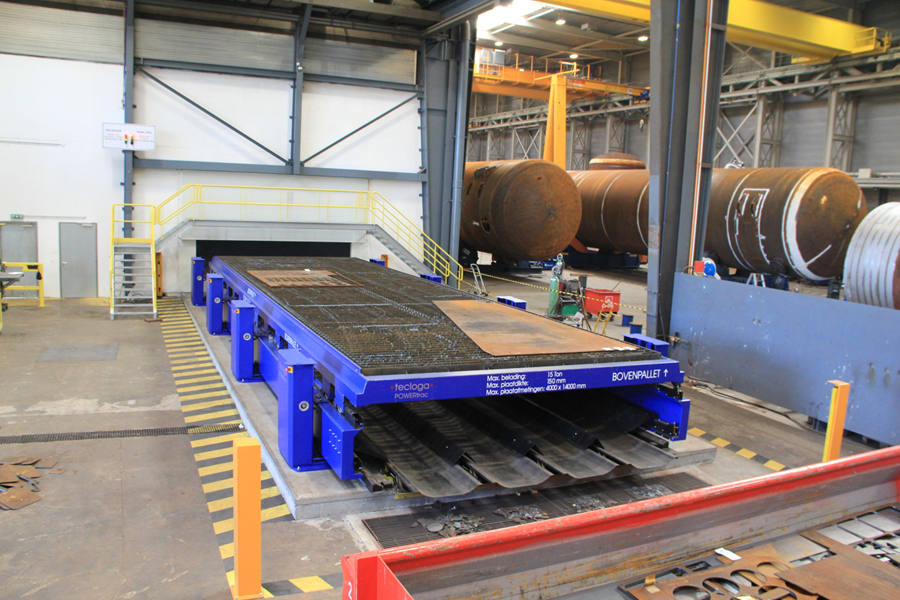
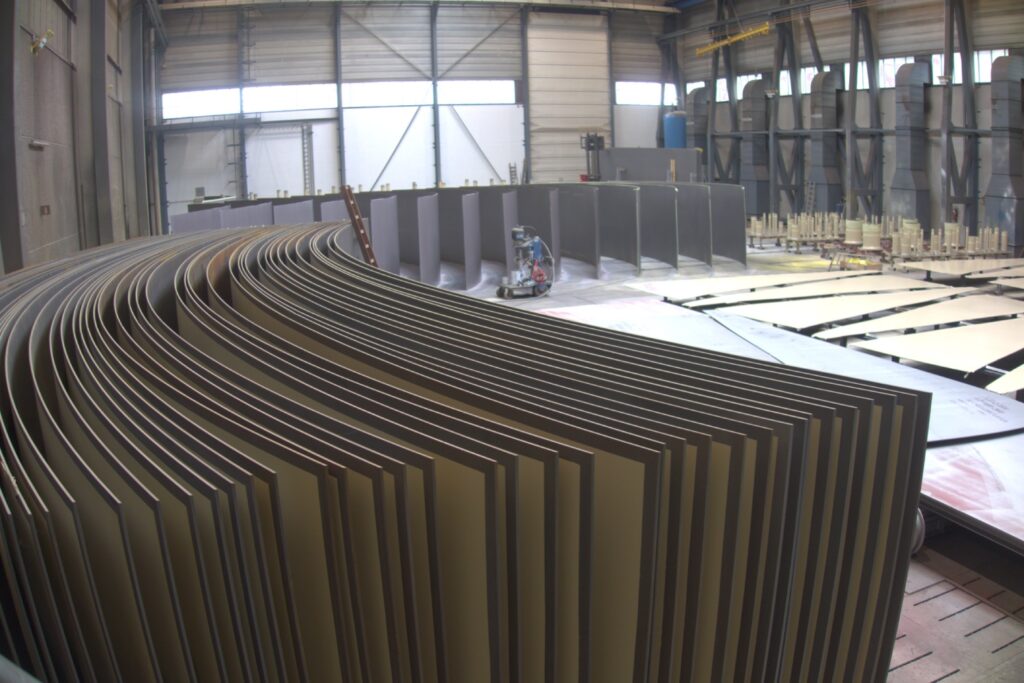
“With a second head, a pneumatic MicroPunch marking unit, engineering can program the marking of plates. With the previous cutting machine, the operator had to stand on the table and apply markings with a handheld device. When it came to plates from which 200 pieces had to be cut, a lot of time was wasted that could not be spent cutting. Now, the marking unit automatically applies a code from the ERP system on the plate, containing the melt number, drawing number, project name, and operator. This way, the plate is ready when it leaves the machine.”
The third head is an oxy-fuel cutting head. This allows the machine to cut plates up to 100 mm thick with ease, ideal for thick-walled pressure vessels or certain accessories.
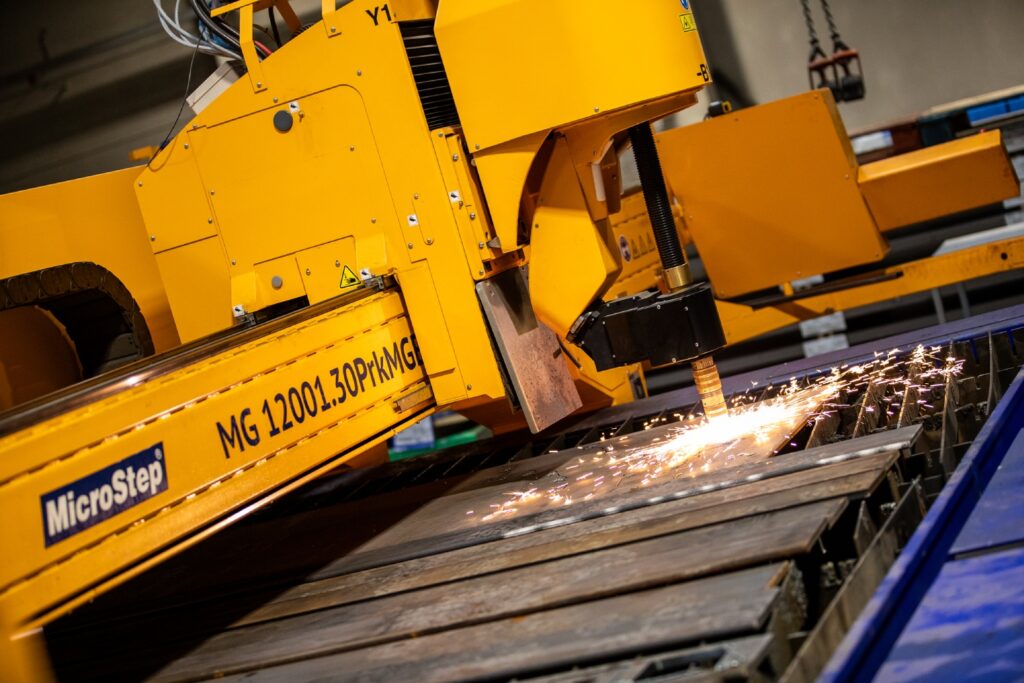
In addition to technology, Engicon also looked at the software. With MicroStep Production Manager (MPM), they have integration with the ERP package, providing real-time insight into stock. This is a great aid in piece and plate management.
Combined with the exchange table system, the software allows Engicon to cut unattended for hours.
“The software integration allows us to pre-scan the barcodes of the plate or nesting to be cut. The operator does this before 9 p.m. He can then place a plate on the exchange table or smaller or larger pieces with long run times on the other table. In the aforementioned marking unit, a laser sensor automatically detects the plate alignment on the table. After placing it on the table, the operator can leave, and the machine can continue cutting unattended for several hours.”
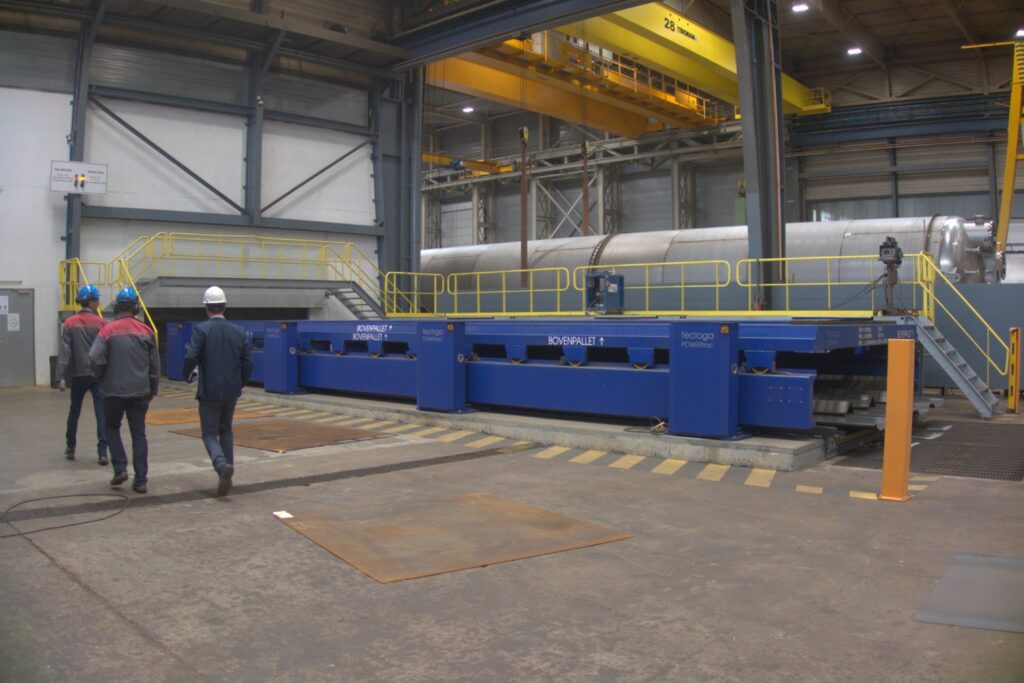
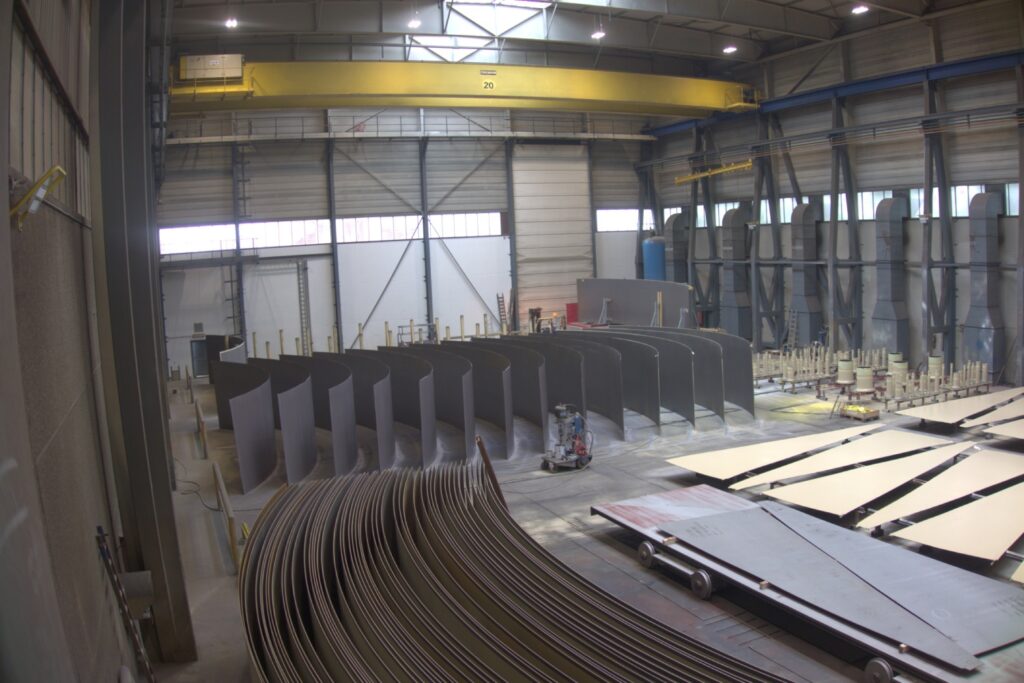
And the collaboration?
“We are very pleased with our choice,” concludes Vandeputte. “The combination of the plasma cutting machine, the exchange table system, and the management software provides us with everything we need to put our further growth ambitions into practice. Wouters Cutting & Welding, as a local player with solid expertise, has guided us well throughout the entire process.”
More cases
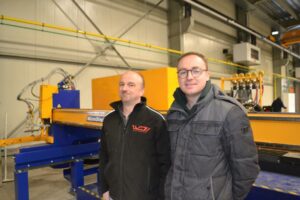
DEOM | MicroStep
Deom’s new MicroStep MasterCut combines high cutting accuracy with speed and automation.
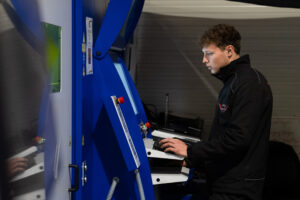
Snijtech | MicroStep
The new MicroStep laser cutting machine at Snijtech makes all the difference for them with its unique bevel control.
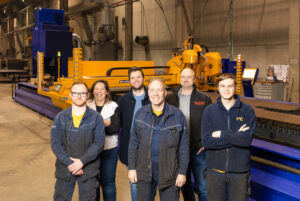
HYE | MG
With the new MicroStep MG, HYE is working more efficiently, flexibly and competitively than ever before.
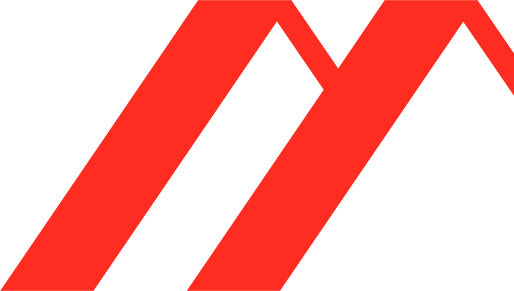
Looking for a cutting or laser machine?
Demo in our showroom or no-obligation appointment?
Or call us +32 3 475 98 25