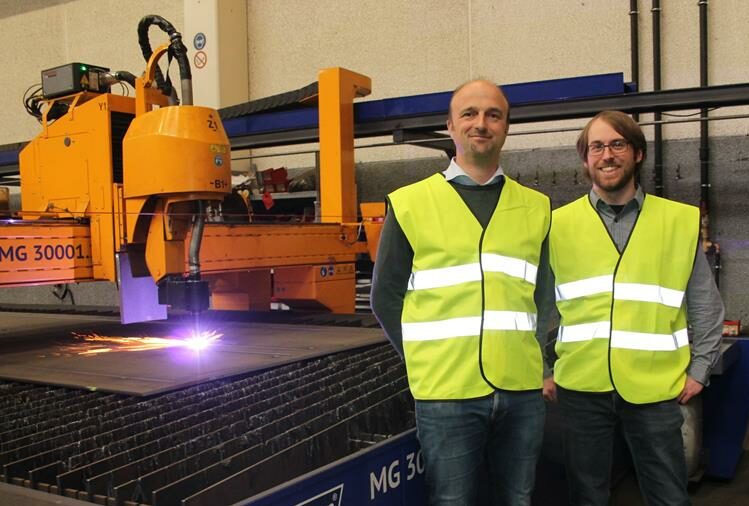
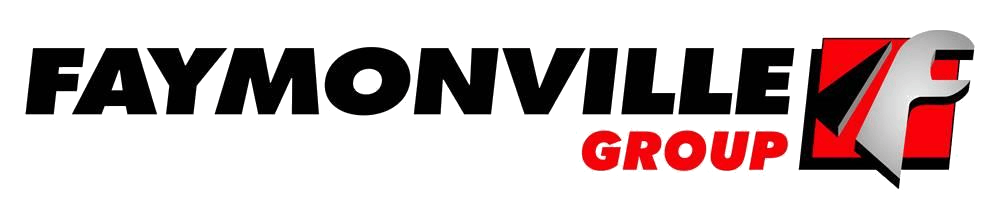
About Faymonville Group
When it comes to heavy and special transport, Faymonville Group is impossible to overlook. What began in 1960 as a blacksmith’s shop in Rocherath, Belgium, quickly grew into a producer of agricultural machinery and transport vehicles.
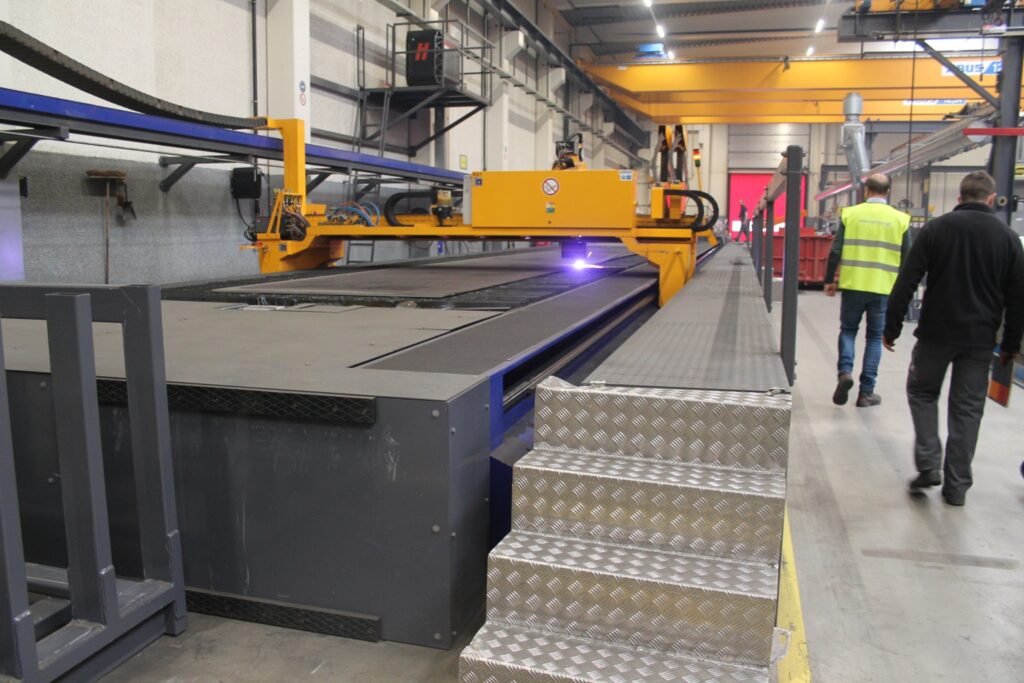
And the numbers don’t lie: it’s a successful business. The Faymonville Group relies on:
- over 1,400 employees;
- 5 production facilities in 4 countries;
- a total production area of 175,000 m²;
- export activities in more than 125 countries;
- 3,000 vehicles produced per year;
- €442 million in revenue in 2023.
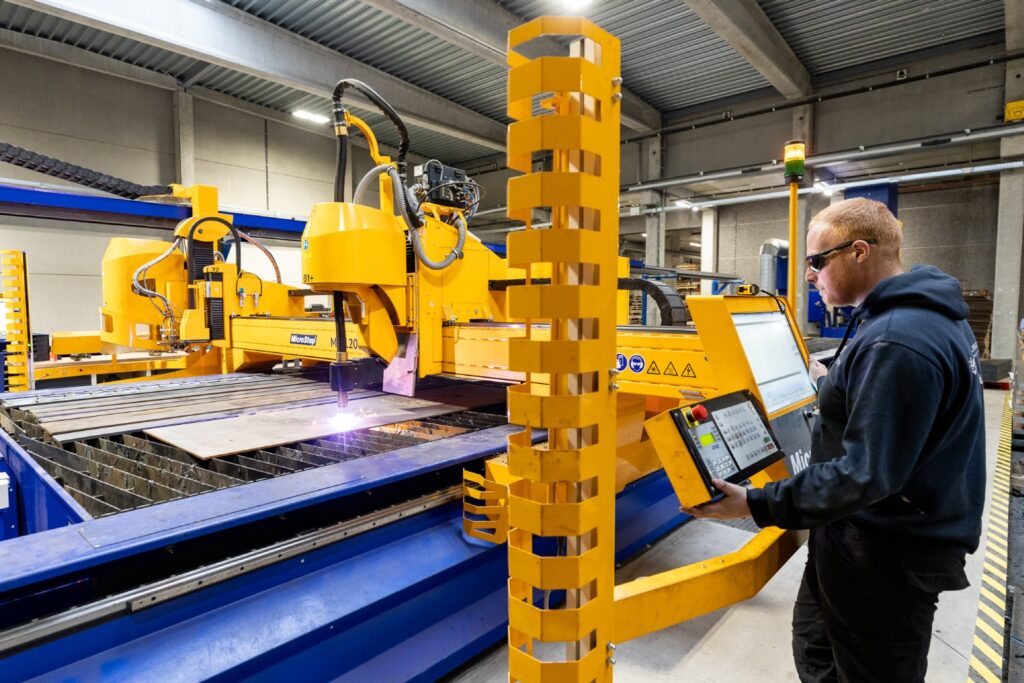
It goes without saying that Wouters Cutting & Welding is a proud partner of Faymonville Group.
Why? Because the entire production of vehicles is done in-house. Everything from plate cutting to assembly and finishing is carried out in their facilities in Luxembourg, Poland, Belgium, Italy, and Russia, ensuring an outstanding level of production quality and effective quality and process controls.
Some time ago, Faymonville Group was in search of two new plate-cutting machines. After a brief search, they turned to Wouters Cutting & Welding and ultimately chose MicroStep cutting machines.
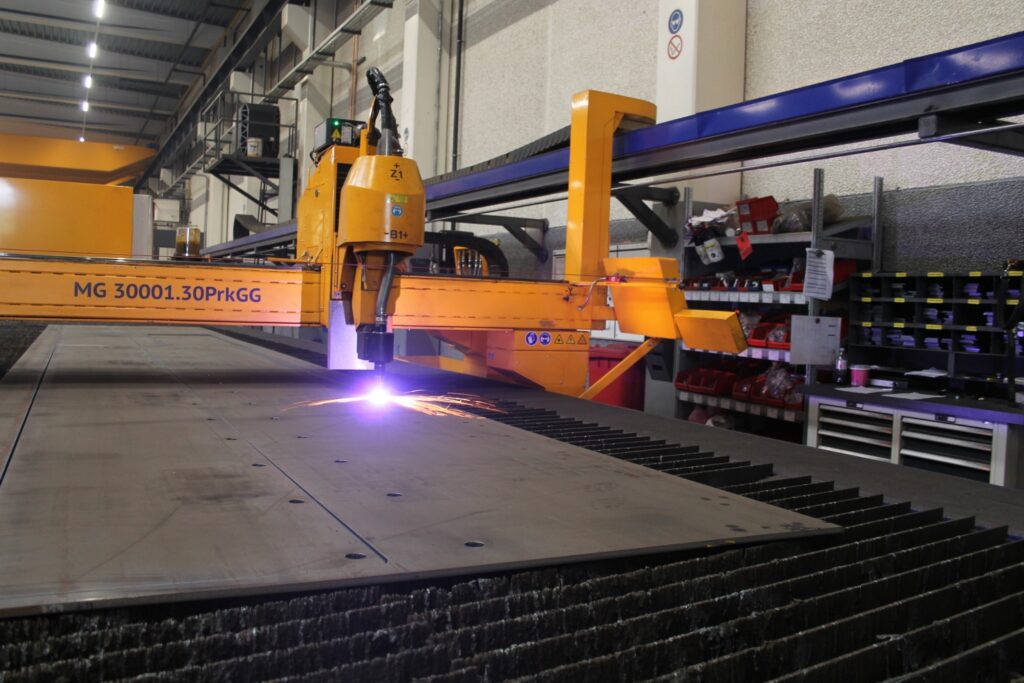
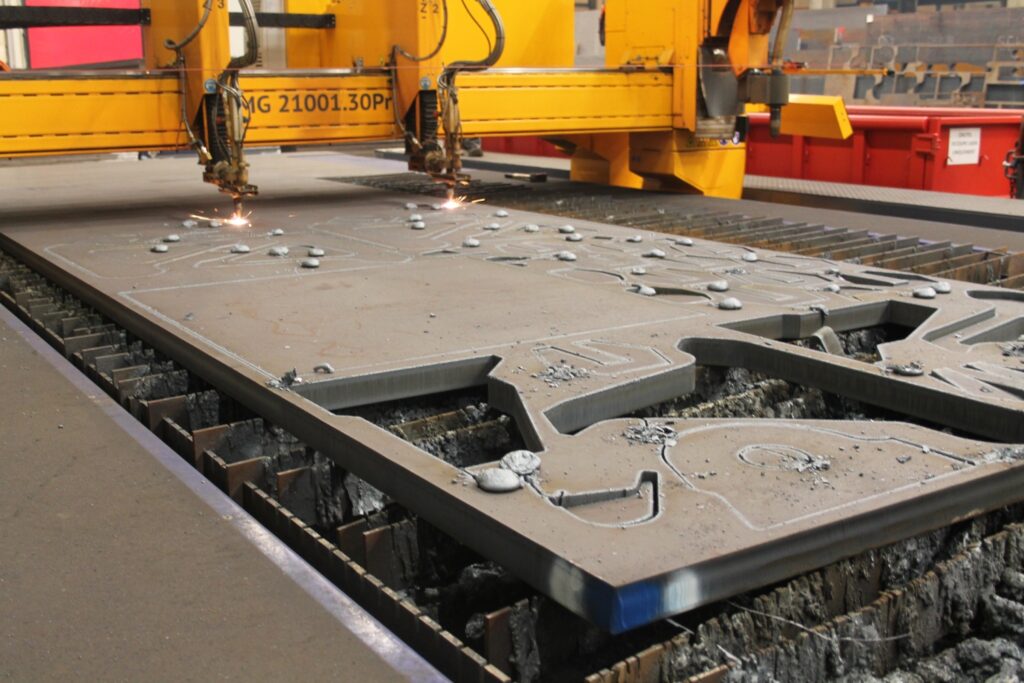
Nic Wouters, managing director at Wouters Cutting & Welding, explains: “The high-end MicroStep MG machine series is designed for extended industrial use and meets the strictest requirements in terms of precision, performance, and ease of use. The machines are customized: from plasma to oxy-fuel cutting, straight and bevel cutting, tube cutting, profile cutting, dome and bend cutting; drilling with automatic tool change; plate positioning with a laser sensor or CCD camera; inkjet or micro-percussion marking. With the special enhanced version, it’s possible to cut up to 250 mm with oxy-fuel.”
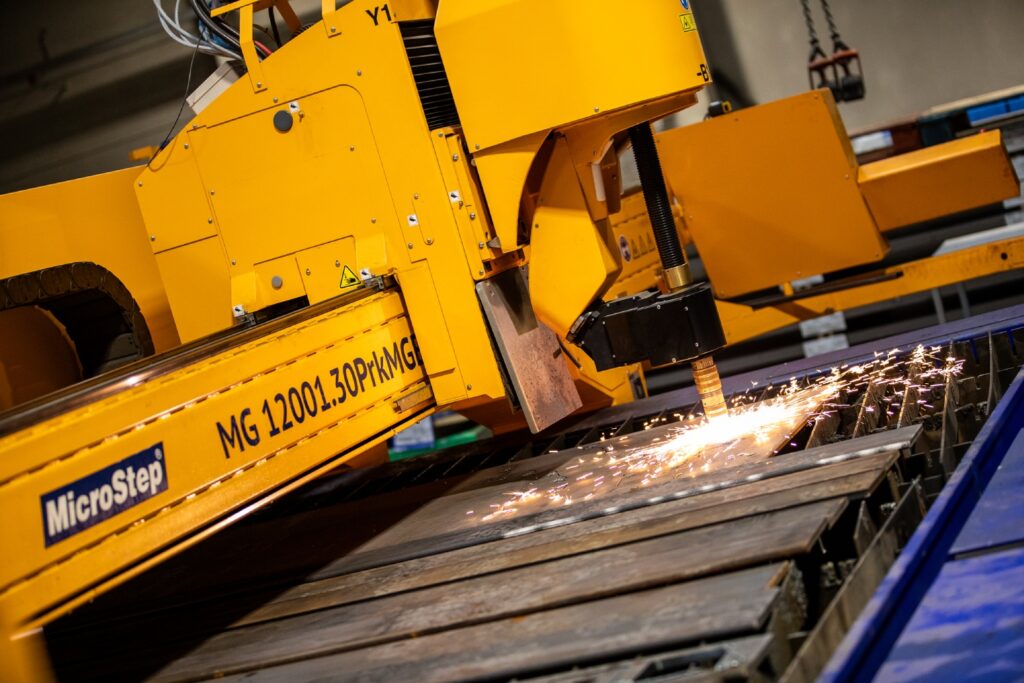
“A new 3,000 m² hall was specially built to house the largest of the two machines,” says Carsten Faber. “This machine is 30 meters long and allows a new plate to be prepared while the other is being cut. This way of working saves a lot of time and makes the process more profitable. So far, four workers have been trained to operate these two machines, with training provided by Wouters Cutting & Welding.”
“The reliability and follow-up of these machines are extremely important to us. Every incident affects production time, and extended downtime is absolutely to be avoided,” explains Carsten Faber. “We know we can always count on a quick response from our supplier. That’s essential for us.”
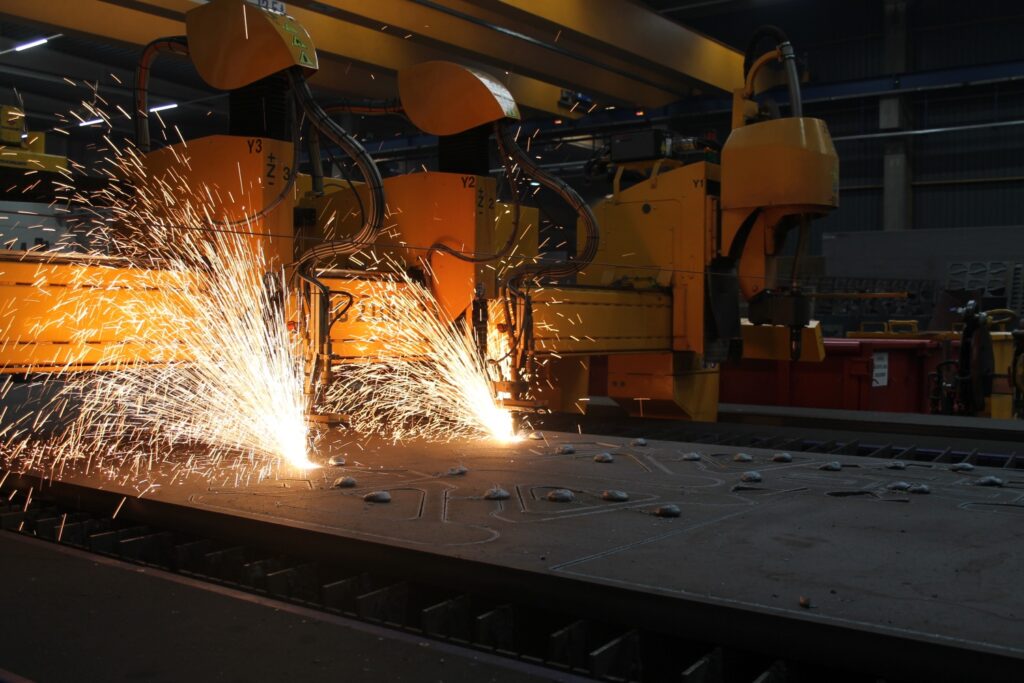
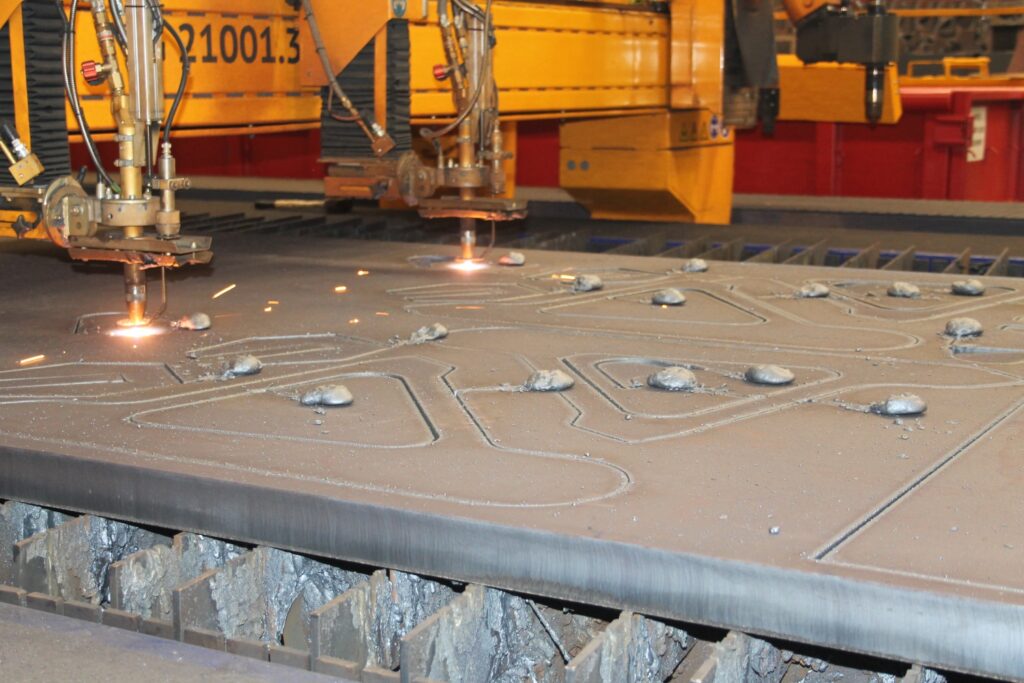

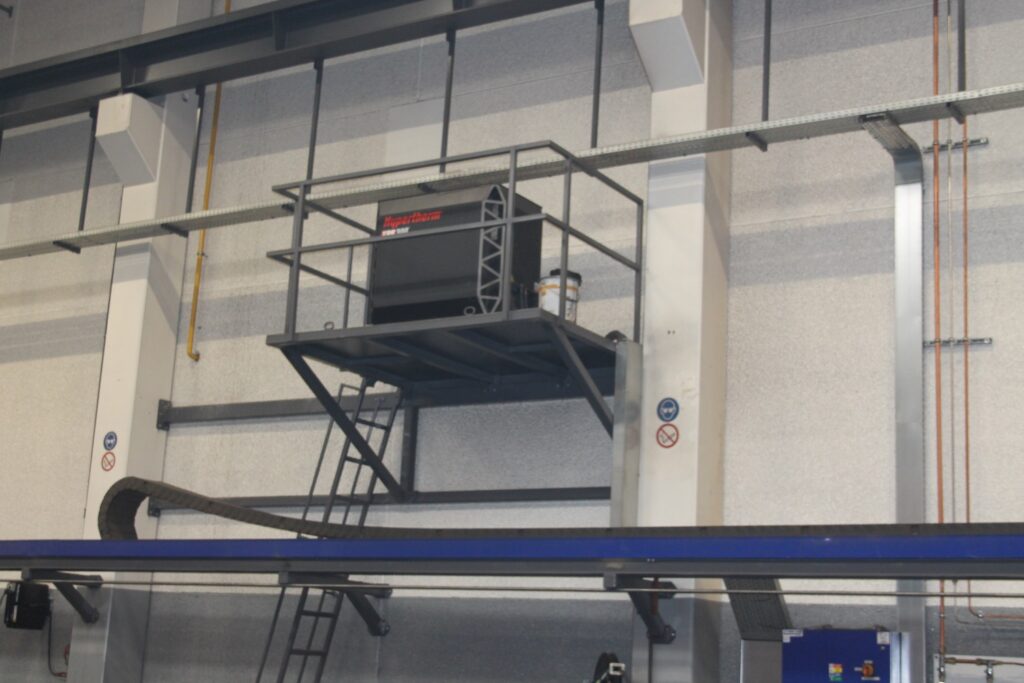
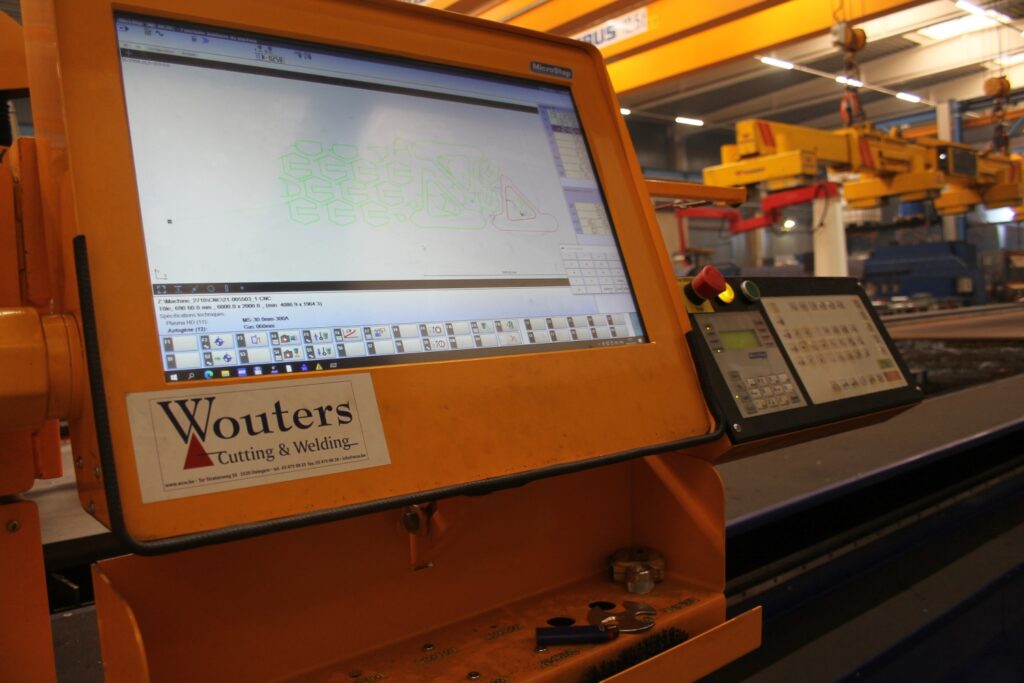
More cases
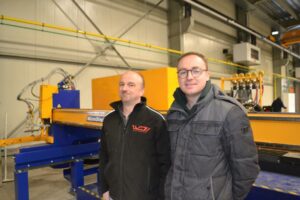
DEOM | MicroStep
Deom’s new MicroStep MasterCut combines high cutting accuracy with speed and automation.
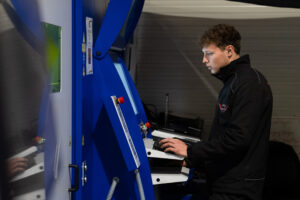
Snijtech | MicroStep
The new MicroStep laser cutting machine at Snijtech makes all the difference for them with its unique bevel control.
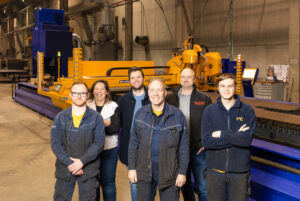
HYE | MG
With the new MicroStep MG, HYE is working more efficiently, flexibly and competitively than ever before.
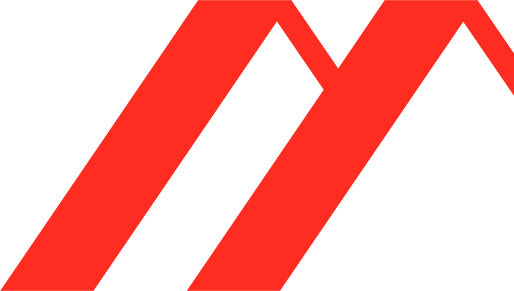
Looking for a cutting or laser machine?
Demo in our showroom or no-obligation appointment?
Or call us +32 3 475 98 25