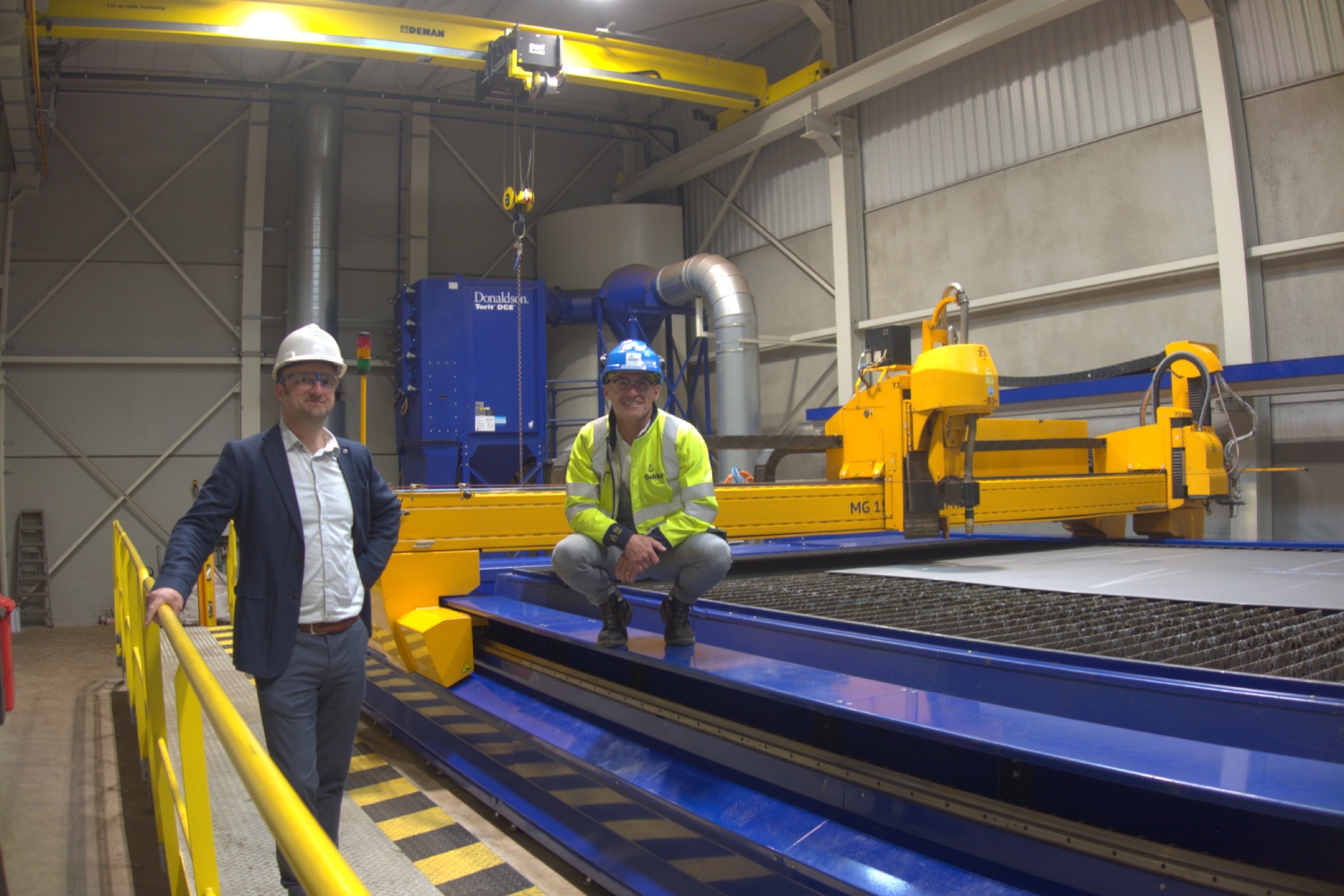
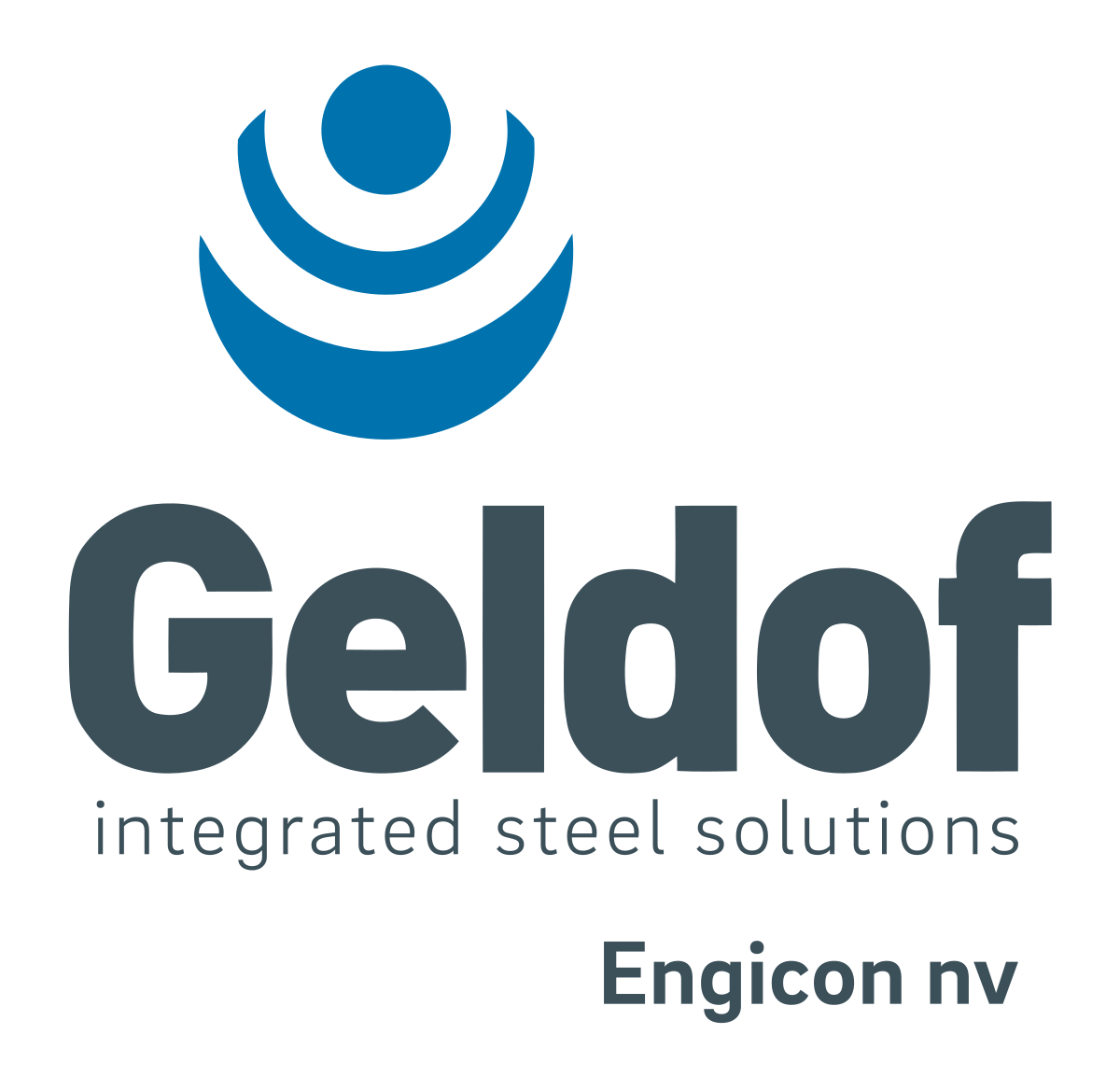
À propos d'Engicon (Geldof)
En 1969, Geldof Metaalconstructie a vu le jour. Avant cela, ils étaient actifs dans l’industrie du lin, mais ils ont perçu le potentiel futur de l’industrie de la transformation des métaux et ont ainsi réorienté leur focus.
Un demi-siècle plus tard, elle a changé de nom pour devenir Engicon, un nom mieux adapté à son ambition internationale. Aujourd’hui, elle est un leader européen dans la construction de solutions de stockage en métal.
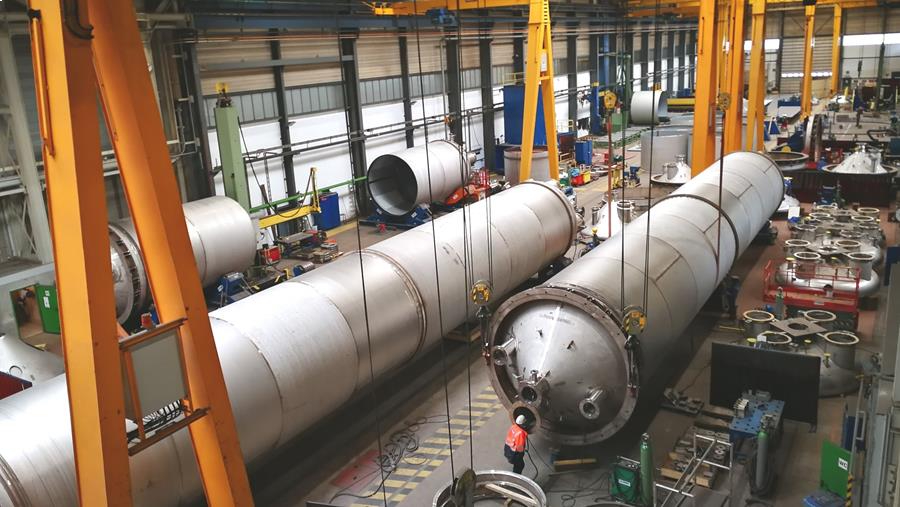
Récemment, Engicon a investi dans une nouvelle machine de découpe plasma et une table de change chez Wouters Cutting & Welding. Dieter Vandeputte, directeur des installations chez Geldof, explique.
“Notre ancienne machine de découpe avait plus de 30 ans et ne pouvait plus offrir la capacité et la qualité nécessaires. De plus, la disponibilité des pièces de rechange n’était plus garantie, ce qui nous a poussés à rechercher une nouvelle machine de découpe. Nous avons brièvement envisagé la technologie laser, mais l’épaisseur de la plupart de nos tôles et la différence de vitesse avec les machines de découpe plasma nous ont finalement fait choisir cette dernière.”
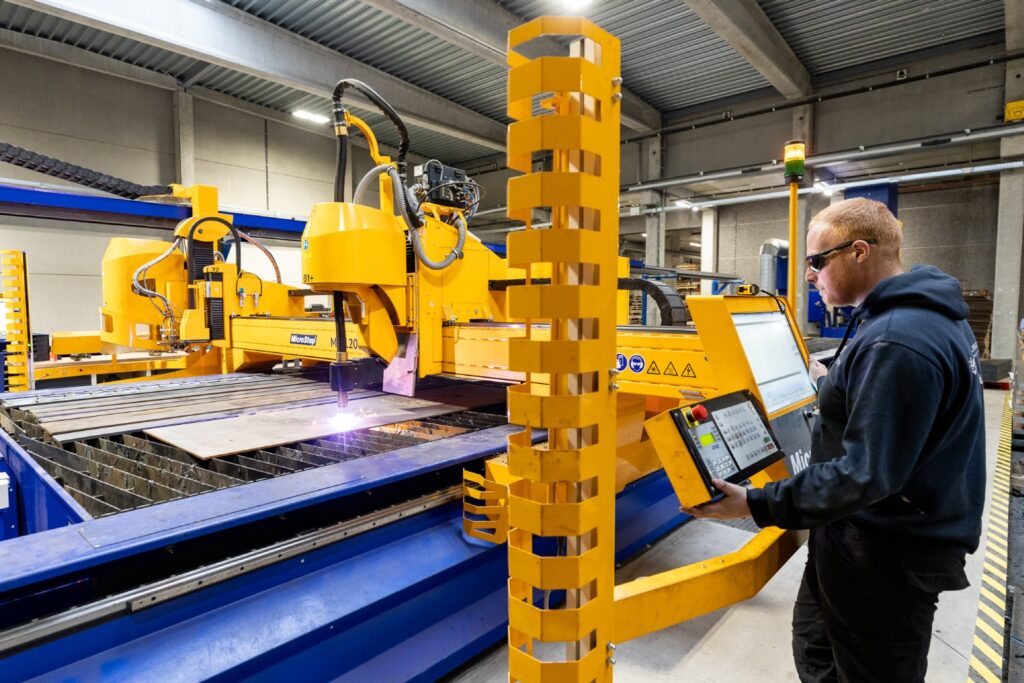
Chez Engicon, ils ont finalement opté pour la machine de découpe plasma MicroStep MG avec une table de transfert Tecloga POWERtrac.
Avec la MicroStep, un monde de nouvelles possibilités s’ouvre. Trois têtes de coupe garantissent une augmentation considérable de la productivité d’Engicon. Et cela ne s’arrête pas là.
“Alors que nous ne pouvions auparavant couper que des contours droits, puis faire le chanfreinage manuellement (ou utiliser une machine séparée), cette fonctionnalité est intégrée dans la nouvelle machine grâce à une tête de biseau rotatif plasma, ce qui nous fait gagner beaucoup de temps”, explique Vandeputte.
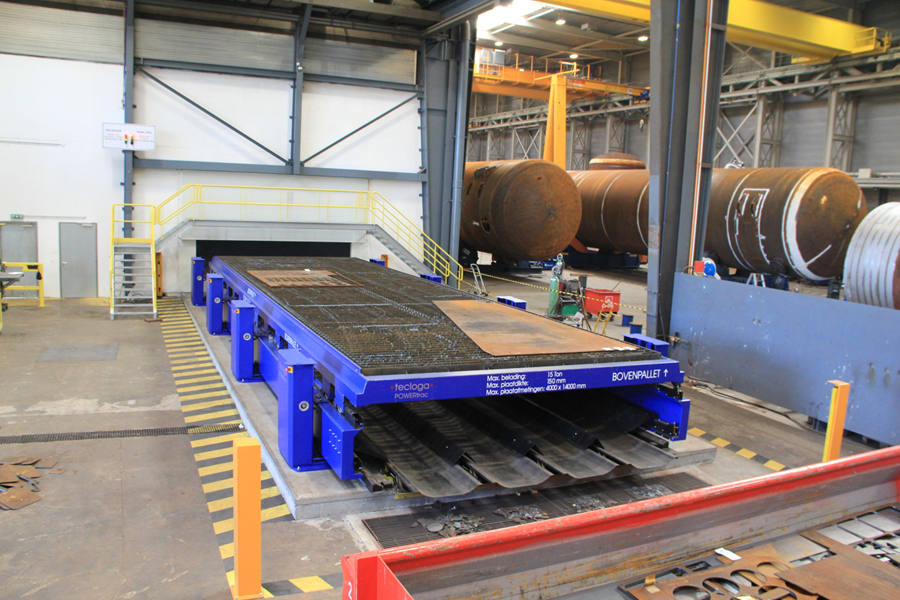
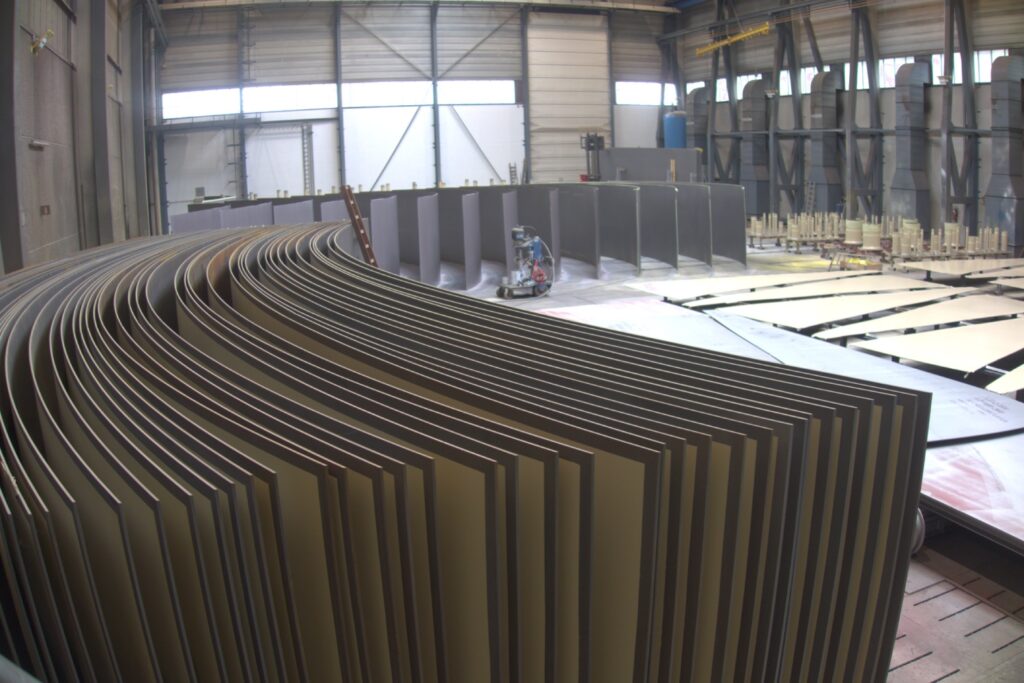
“Avec une deuxième tête, une unité de marquage pneumatique MicroPunch, l’ingénierie peut programmer le marquage des tôles. Avec l’ancienne machine, l’opérateur devait se tenir sur la table et marquer manuellement avec un appareil portatif. Lorsque des tôles devaient produire 200 pièces, cela prenait beaucoup de temps que nous ne pouvions consacrer à la découpe. Désormais, l’unité de marquage applique automatiquement, via le système ERP, un code sur la tôle qui contient le numéro de fusion, le numéro de dessin, le nom du projet et l’opérateur. Ainsi, la tôle est prête lorsqu’elle quitte la machine.”
La troisième tête est une tête de découpe autogène. Cela permet à la machine de découper facilement des tôles jusqu’à 100 mm. Idéale pour les récipients à pression épais ou certains accessoires.
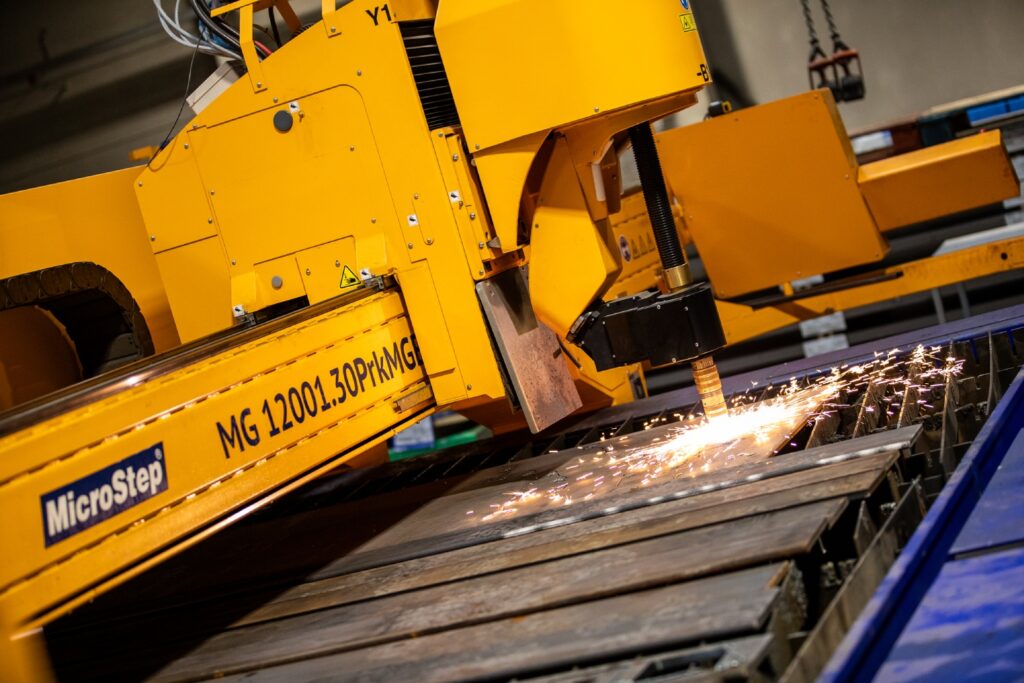
En plus des technologies, Engicon a également examiné le logiciel. Avec MicroStep Production Manager (MPM), ils disposent d’une intégration avec le package ERP. Cela permet une vue en temps réel du stock, ce qui est d’une grande aide pour la gestion des pièces et des tôles.
En combinaison avec le système de table de transfert, le logiciel permet à Engicon de découper pendant des heures sans surveillance.
“La connexion logicielle permet de scanner à l’avance les codes-barres de la tôle ou du modèle de découpe à réaliser. L’opérateur fait cela avant 21 h. Ensuite, il peut placer une tôle sur la table de transfert, ou sur l’autre table des pièces plus petites ou plus grandes avec des temps de cycle longs. Dans l’unité de marquage mentionnée précédemment, un capteur laser détecte automatiquement l’alignement de la tôle sur la table. Après le placement sur la table, l’opérateur peut partir et la machine peut continuer à découper sans surveillance pendant plusieurs heures.”
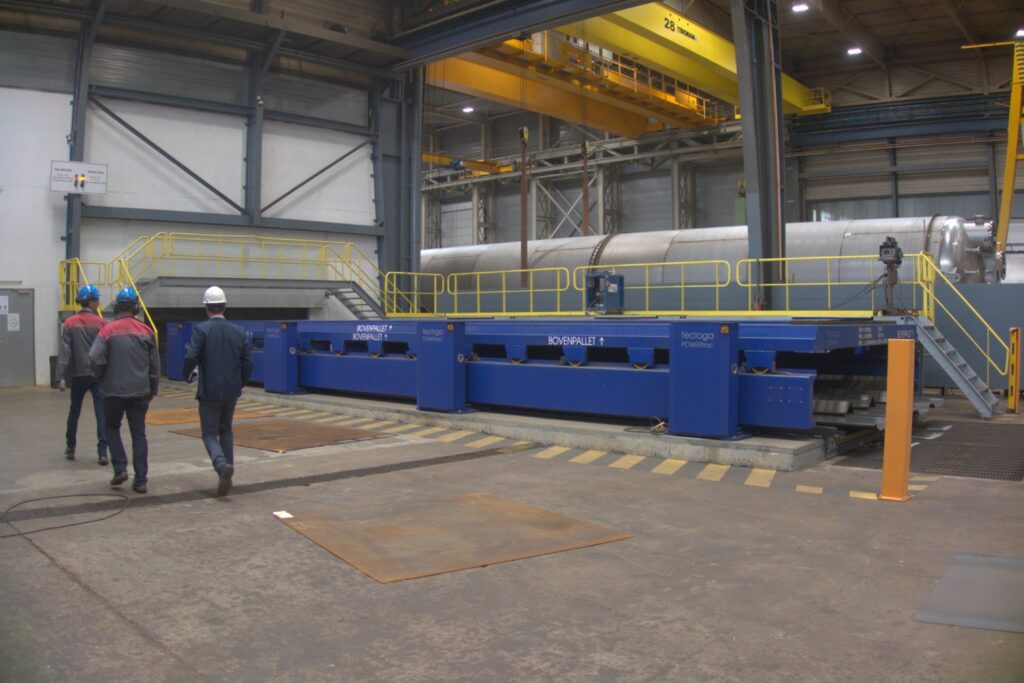
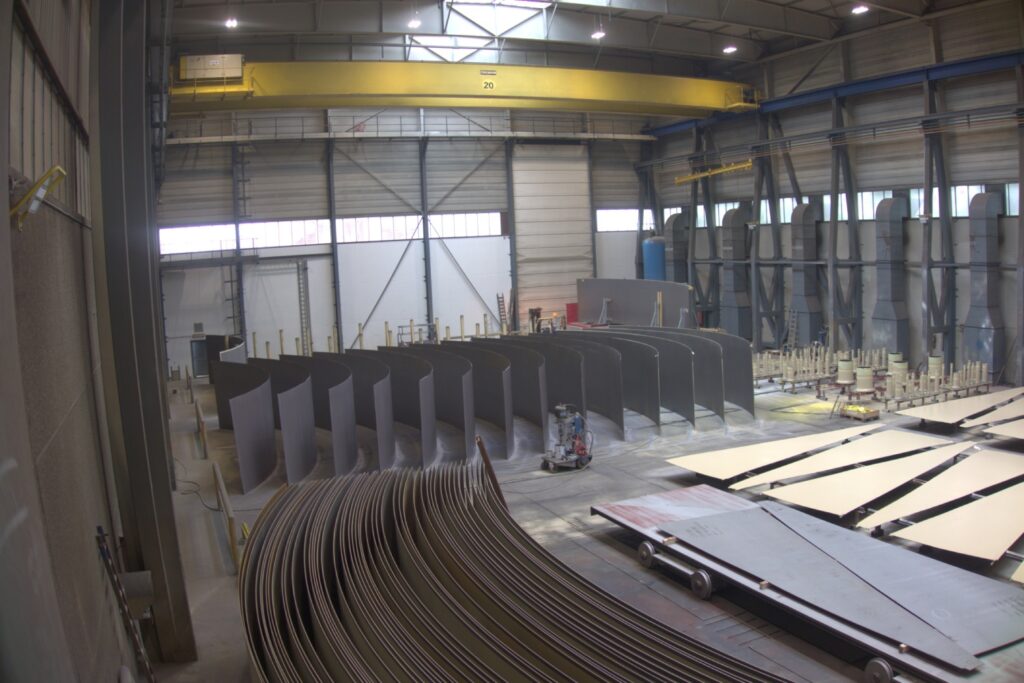
Et la collaboration ?
“Nous sommes très satisfaits de notre choix”, conclut Vandeputte. “La combinaison de la machine de découpe plasma, du système de table de transfert et du logiciel de gestion nous offre tout ce dont nous avons besoin pour concrétiser nos ambitions de croissance. Wouters Cutting & Welding, en tant qu’acteur local possédant un savoir-faire solide, nous a bien accompagnés tout au long du processus.”
Plus de cas
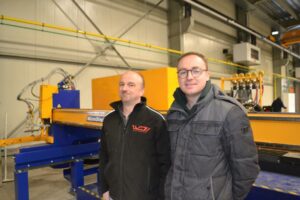
DEOM | MicroStep
La nouvelle MicroStep MasterCut de Deom allie une grande précision de coupe à la vitesse et à l’automatisation.
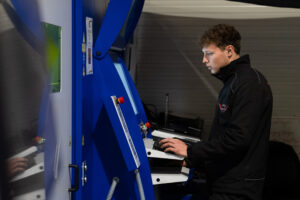
Snijtech | MicroStep
La nouvelle machine de découpe laser MicroStep de Snijtech fait la différence grâce à son système unique de contrôle de chanfrein.
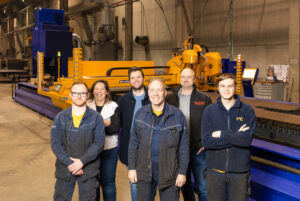
HYE | MG
Grâce à la nouvelle MicroStep MG, HYE travaille de manière plus efficace, plus flexible et plus compétitive que jamais.
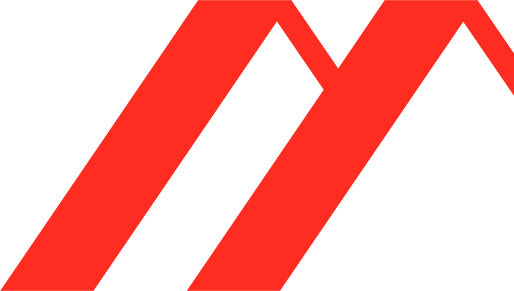
Vous cherchez une solution de découpe ou de laser ?
Démonstration en salle d’exposition ou rendez-vous sans engagement ?
Ou appelez-nous au numéro suivant +32 3 475 98 25